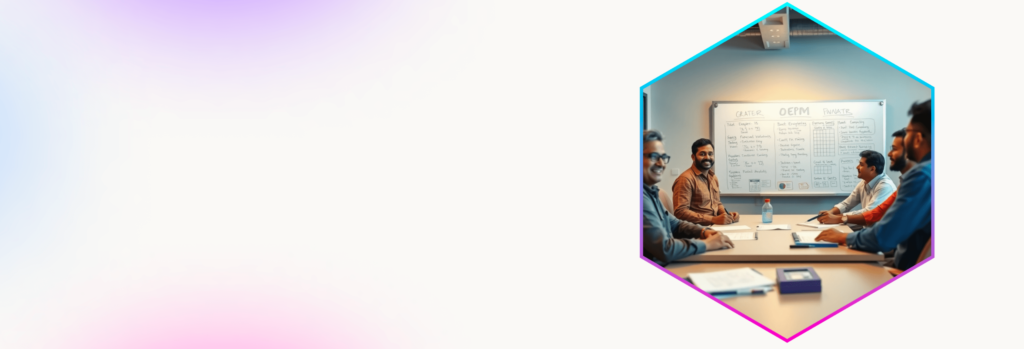
TPM: Blueprint for
Success
Table of Contents
ToggleTotal Productive Maintenance: Benefits, Tools, Techniques, and Implementation Strategies
As manufacturing operations become more complex, Total Productive Maintenance (TPM) has become an essential philosophy to ensure efficient, cost-effective, and high-quality production. TPM focuses on maximizing equipment effectiveness, reducing downtime, and involving all employees in continuous improvement efforts. This comprehensive guide provides an overview of TPM principles, benefits, tools and techniques, implementation strategies, and the role of CMMS in TPM rollouts.
What is TPM?
Total Productive Maintenance (TPM) is a maintenance philosophy that aims to maximize equipment effectiveness, minimize downtime, and increase productivity, quality control, and safety in manufacturing operations. TPM is based on the principle that everyone in the organization is responsible for equipment maintenance, and that maintenance should be proactive, not reactive. TPM focuses on a holistic approach to maintenance that involves all employees, from operators to managers, and emphasizes continuous improvement and teamwork.
Objectives of TPM
The objectives of Total Productive Maintenance (TPM) are critical to achieving efficiency and success in manufacturing operations. Here’s a breakdown of the objectives:
1. Maximize equipment effectiveness
TPM aims to ensure that all equipment is operating at peak efficiency, reducing downtime and increasing productivity. By doing so, organizations can improve customer satisfaction and reduce costs associated with equipment inefficiencies.
2. Minimize downtime
TPM strives to proactively identify and address potential equipment problems before they cause downtime. This approach to maintenance can significantly reduce downtime and repair costs.
3. Reduce costs associated with maintenance and repair
TPM aims to improve equipment reliability, reduce the need for costly repairs, and ultimately lower maintenance and repair costs.
4. Improve quality control and product consistency
TPM ensures that equipment is functioning properly, and products meet or exceed quality standards. Consistent product quality leads to increased customer satisfaction and business growth.
5. Enhance safety and reduce the risk of accidents
TPM focuses on identifying and addressing potential safety hazards, reducing the risk of accidents and injuries to employees.
6. Engage all employees in continuous improvement efforts
By involving all employees in continuous improvement efforts, TPM empowers them to identify and address equipment problems and inefficiencies. This employee involvement can lead to significant improvements in equipment effectiveness, productivity, and quality control.
Key principles of TPM
The Key Principles of TPM are
- Equipment should be designed for reliability and maintainability: TPM emphasizes the importance of designing equipment with reliability and maintainability in mind. This ensures that equipment is easy to maintain, reducing downtime and repair costs.
- Maintenance should be proactive, not reactive: TPM focuses on a proactive approach to maintenance, identifying and addressing potential equipment problems before they cause downtime or safety hazards.
- Operators should be involved in maintenance activities: TPM encourages operators to be involved in maintenance activities, empowering them to identify and address equipment problems.
- Equipment should be continuously improved: TPM emphasizes the importance of continuously improving equipment, using tools such as Root Cause Analysis and Data Analysis to identify and address equipment problems.
- Teamwork and communication are essential for TPM success: TPM requires teamwork and communication among all employees, from operators to managers, to achieve success. Effective communication ensures that everyone is working towards the same goals and objectives.
By following these key principles, organizations can improve equipment effectiveness, reduce downtime, lower maintenance and repair costs, improve product quality, increase safety, and promote a culture of continuous improvement.
Role of TPM in Streamlining Manufacturing Organisations
TPM plays a vital role in streamlining manufacturing organizations by:
- Reducing downtime and increasing equipment effectiveness: TPM’s focus on proactive maintenance helps identify potential equipment problems before they cause downtime, leading to increased equipment effectiveness and reduced costs.
- Improving product quality and consistency: TPM’s emphasis on equipment reliability and maintainability ensures that products meet or exceed quality standards, leading to increased customer satisfaction.
- Increasing productivity and efficiency: TPM’s focus on continuous improvement leads to increased productivity and efficiency by eliminating waste, optimizing processes, and improving equipment performance.
- Reducing maintenance and repair costs: TPM’s proactive maintenance approach reduces the need for costly repairs, leading to lower maintenance and repair costs.
- Engaging all employees in continuous improvement efforts: TPM empowers all employees to identify and address equipment problems, promoting a culture of continuous improvement and ensuring that everyone is working towards the same goals and objectives.
Benefits of TPM for Manufacturing Operations
TPM offers a wide range of benefits for manufacturing operations, including:
- Increased equipment effectiveness and productivity
- Reduced downtime and maintenance costs
- Improved product quality and consistency
- Enhanced safety and reduced risk of accidents
- Increased employee engagement and teamwork
- Continuous improvement and innovation
- Increased customer satisfaction and loyalty
8 Pillars of TPM
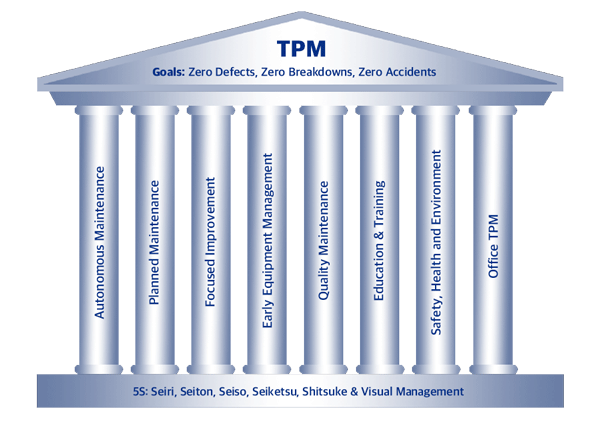
The 8 Pillars of TPM are:
Total Productive Maintenance (TPM) is based on eight pillars, which are essential for achieving its objectives. Here is a brief description of each pillar:
Autonomous Maintenance
Operators are trained to perform routine maintenance tasks, such as cleaning and lubricating, reducing the workload of maintenance personnel and increasing equipment effectiveness.
Focussed Maintenance
A continuous improvement approach that focuses on improving individual processes rather than the entire system. It involves small, incremental changes made by employees at all levels of an organization to improve efficiency, quality, and safety.
Planned Maintenance
Maintenance activities are planned and scheduled in advance, ensuring that maintenance personnel have the necessary resources and equipment to perform their tasks efficiently.
Quality Maintenance
Quality is built into the maintenance process, ensuring that equipment is maintained to meet or exceed quality standards.
Early Equipment Management
Equipment is designed for reliability and maintainability, and potential problems are identified and addressed in the design phase.
Education and Training
All employees receive training on TPM principles and practices, empowering them to identify and address equipment problems.
Office TPM
TPM principles are applied to administrative processes, such as planning and scheduling, to improve efficiency and effectiveness.
Safety, Health, and Environment
TPM emphasizes safety, health, and environmental considerations, ensuring that maintenance activities are performed safely and with minimal impact on the environment.
Each of these pillars focuses on a specific aspect of TPM implementation, and together they create a holistic approach to equipment maintenance and improvement.
By implementing these Eight Pillars of TPM, organizations can achieve its objectives of maximizing equipment effectiveness, reducing downtime, lowering maintenance and repair costs, improving product quality, increasing safety, and promoting a culture of continuous improvement.
Tools and Techniques used in TPM
TPM uses a variety of tools and techniques to achieve its objectives, including:
- Root Cause Analysis: A problem-solving technique used to identify the underlying cause of equipment problems and prevent recurrence.
- Data Analysis: Using data to identify patterns and trends that can be used to improve equipment performance and prevent downtime.
- Standard Operating Procedures (SOPs): Written procedures that describe how to perform maintenance tasks and ensure consistency and quality.
- Preventive Maintenance: Regular maintenance tasks performed to prevent equipment failure and prolong equipment life.
- Kanban: A visual management tool used to control inventory levels and ensure that equipment and materials are available when needed.
- 5S: A workplace organization technique used to improve efficiency and productivity by organizing the workplace and eliminating waste.
- Standard Work: A process improvement technique used to establish a standard way of performing tasks to ensure consistency and quality.
- Visual Management: The use of visual aids, such as signs, labels, and displays, to communicate important information and improve workplace organization.
- Single-Minute Exchange of Dies (SMED): A process improvement technique used to reduce equipment changeover time and increase production efficiency.
- Asset Management: A system for managing equipment throughout its lifecycle, from acquisition to disposal, to ensure that it is reliable, maintainable, and optimized for performance.
- Quality Control: A set of techniques used to measure and control product quality, ensuring that products meet or exceed customer expectations.
- Problem-Solving: A systematic approach to identifying and solving problems, using tools and techniques such as the 5 Whys and Fishbone Diagrams to identify root causes and develop solutions.
- Continuous Improvement: A philosophy of constantly striving for improvement, using techniques such as Kaizen to make small, incremental changes that add up to significant improvements over time.
These tools and techniques are essential to the success of TPM, allowing organizations to identify and address equipment problems, improve efficiency and productivity, and maintain high levels of quality and safety.
TPM and other Maintenance Management Philosophies
TPM and Lean Manufacturing
TPM and Lean Manufacturing share similar objectives, including reducing waste, improving efficiency, and enhancing customer value. TPM focuses on equipment maintenance and effectiveness, while Lean Manufacturing focuses on process improvement and waste reduction. Both philosophies emphasize employee involvement and continuous improvement.
TPM and Six Sigma
TPM and Six Sigma both focus on continuous improvement and reducing defects and waste. Six Sigma uses statistical tools and techniques to improve quality control, while TPM emphasizes equipment maintenance and reliability. Both philosophies require employee involvement and a commitment to continuous improvement.
TPM and RCM
TPM and Reliability-Centered Maintenance (RCM) both focus on maximizing equipment effectiveness and reliability. RCM emphasizes a risk-based approach to maintenance, while TPM emphasizes a holistic approach that involves all employees. Both philosophies require continuous improvement and a commitment to proactive maintenance.
TPM and TQM
TPM and Total Quality Management (TQM) share similar objectives, including improving quality control and customer satisfaction. TQM focuses on process improvement and quality control, while TPM focuses on equipment maintenance and effectiveness. Both philosophies require employee involvement and a commitment to continuous improvement.
TPM and World Class Manufacturing
TPM is an essential component of World Class Manufacturing, which focuses on creating a culture of continuous improvement and excellence in manufacturing operations. World Class Manufacturing emphasizes employee involvement, waste reduction, and quality control, and TPM is essential for maximizing equipment effectiveness and reliability.
Implementing TPM in your Manufacturing Process
Implementing TPM in your manufacturing process requires a strategic approach that involves the following steps:
- Identify equipment and process problems
- Engage all employees in TPM implementation
- Develop a TPM implementation plan
- Implement the 8 Pillars of TPM
- Monitor and continuously improve TPM effectiveness
Implementing TPM requires a significant commitment to employee involvement, continuous improvement, and a proactive approach to equipment maintenance.
Challenges in TPM Rollout and Mitigation Plan
Implementing TPM can be challenging, and organizations may face various obstacles during the rollout. These challenges can include resistance to change, lack of employee buy-in, inadequate resources, and insufficient training. To mitigate these challenges, organizations should focus on clear communication, employee engagement, and training, as well as creating a culture of continuous improvement and teamwork. Organizations should also allocate sufficient resources and provide adequate training to ensure that TPM implementation is successful.
Role of CMMS in TPM Rollout
Computerized Maintenance Management Systems (CMMS) can play a vital role in TPM implementation by:
- Tracking equipment maintenance and repair history
- Monitoring equipment performance and effectiveness
- Identifying equipment problems and potential failures
- Providing data for continuous improvement and analysis
- Streamlining maintenance and repair processes
CMMS can help organizations implement TPM more effectively and efficiently by providing real-time data and analysis, which is essential for continuous improvement.
Future of TPM
The future of TPM is bright, as manufacturing operations become more complex and require more efficient, cost-effective, and high-quality production. TPM will continue to play a vital role in achieving these objectives by emphasizing employee involvement, continuous improvement, and a proactive approach to equipment maintenance. The integration of new technologies, such as artificial intelligence and the Internet of Things, will also play a significant role in the future of TPM, enabling organizations to monitor and optimize equipment performance in real-time.
Total Productive Maintenance (TPM) is a maintenance philosophy that aims to maximize equipment effectiveness, minimize downtime, and increase productivity, quality control, and safety in manufacturing operations. TPM is based on the principle that everyone in the organization is responsible for equipment maintenance, and that maintenance should be proactive, not reactive. TPM focuses on a holistic approach to maintenance that involves all employees, from operators to managers, and emphasizes continuous improvement and teamwork. Implementing TPM requires a significant commitment to employee involvement, continuous improvement, and a proactive approach to equipment maintenance.
Computerized Maintenance Management Systems (CMMS) can play a vital role in TPM implementation by providing real-time data and analysis, which is essential for continuous improvement. The future of TPM is bright, as manufacturing operations become more complex and require more efficient, cost-effective, and high-quality production.
Request a one-one demo with our solution engineering team.
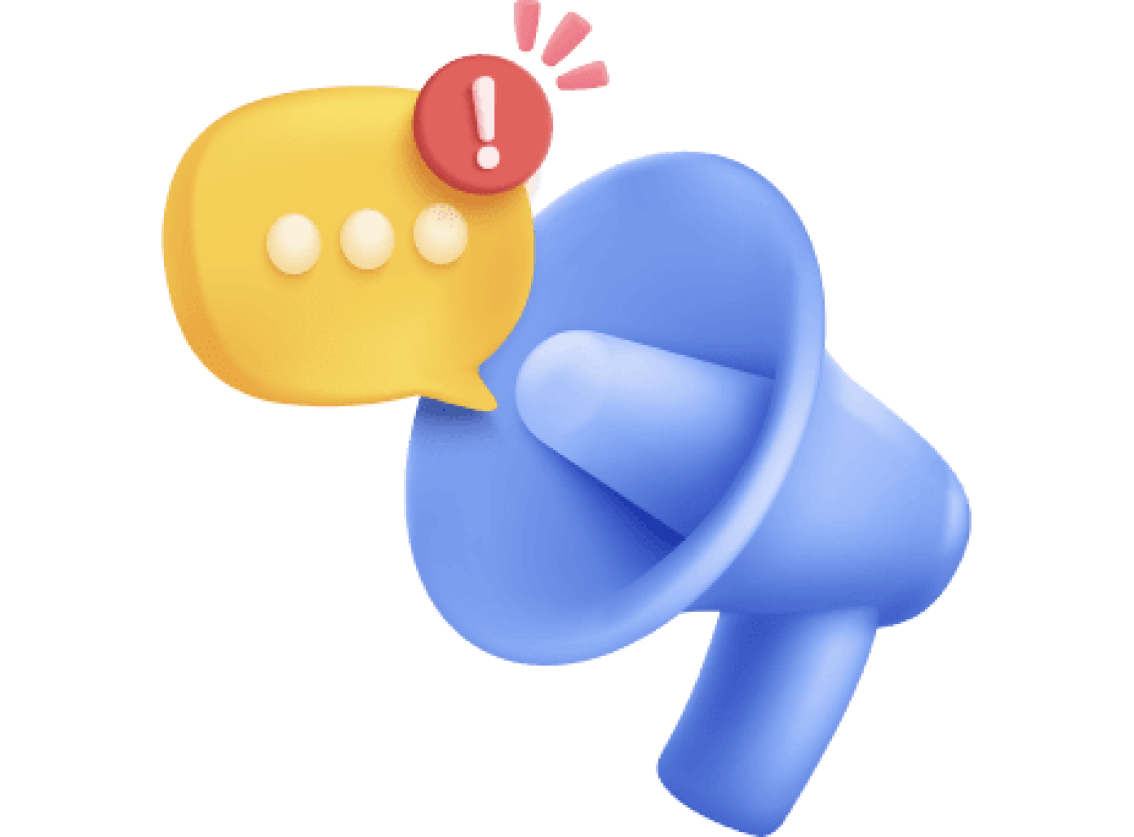
Request a one-one demo with our solution engineering team.