Unleash the Power of Smart Preventive Maintenance with MaintWiz CMMS
Transform your maintenance operations, boost asset longevity, and drive operational excellence. Our AI-enhanced CMMS solution puts you in control, delivering unparalleled efficiency and cost savings.
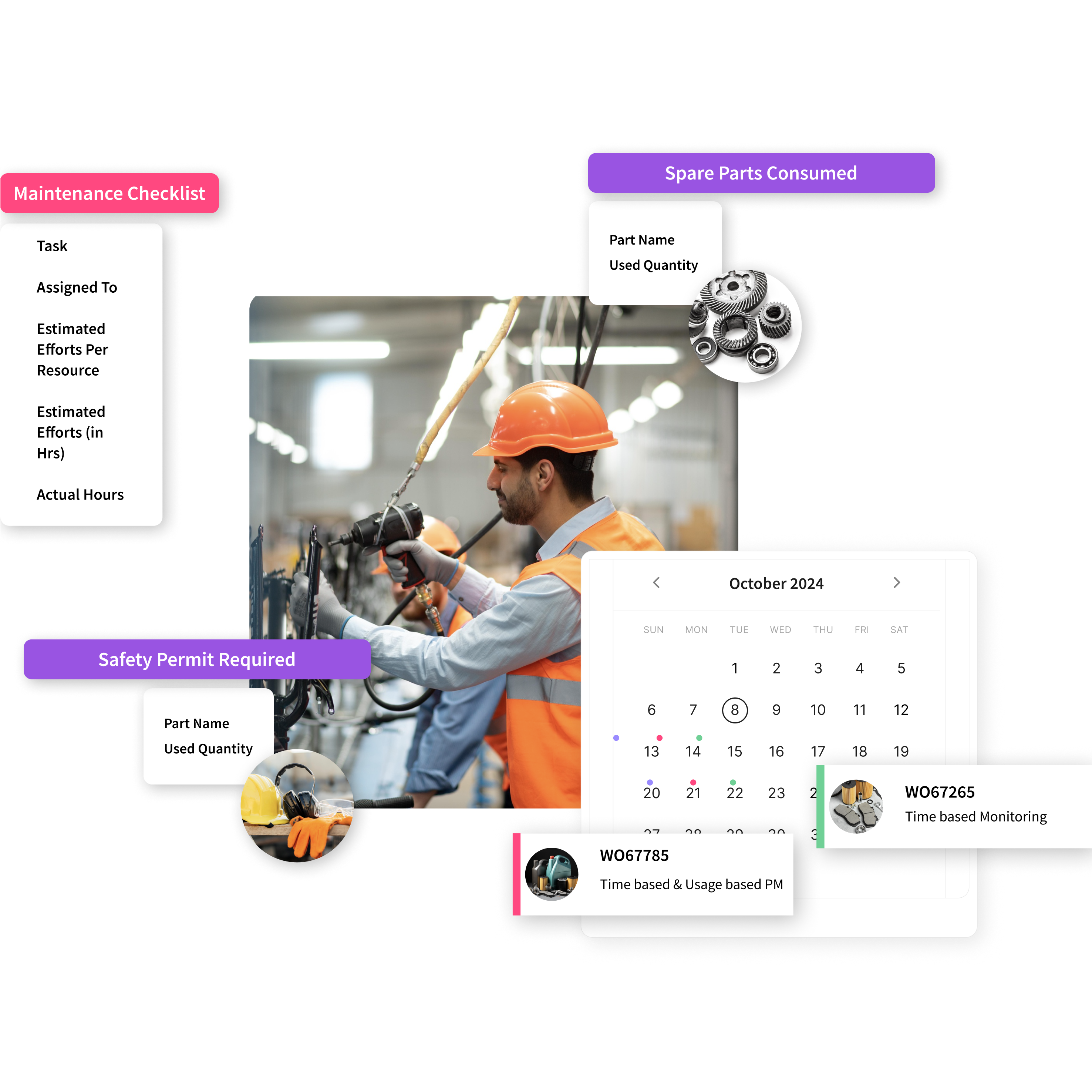
Preventive Maintenance
Dive into Detailed Product Information and address your common queries.
Speak to a Specialist
Get personalised advice from our experts
Comprehensive Preventive Maintenance Management:
Your Key to Asset Optimization
MaintWiz CMMS revolutionizes preventive maintenance, empowering you to maximize asset performance and lifespan. Our intelligent system streamlines operations, ensuring your maintenance strategy stays ahead of the curve.
Automated Scheduling: Precision Timing for Peak Efficiency
Say goodbye to maintenance guesswork. MaintWiz’s AI-driven scheduling engine optimizes your maintenance calendar, integrating seamlessly with production systems to keep your assets in prime condition without disrupting operations.
Customizable Maintenance Plans: Tailored Strategies for Every Asset
One size doesn’t fit all in maintenance. Our platform enables you to craft bespoke preventive maintenance plans, leveraging historical data and risk analysis to ensure each asset receives the care it needs, when it needs it.
Real-time Task Tracking: Visibility that Drives Results
Keep your finger on the pulse of maintenance activities. MaintWiz provides instant visibility into task progress, empowering your team to respond swiftly to changing priorities and ensure no maintenance task falls through the cracks.
Mobile Accessibility: Empower Your Team On-the-Go
Maintenance doesn’t wait, and neither should you. Our mobile-friendly interface ensures your team has critical information at their fingertips, enabling rapid response and informed decision-making from anywhere, at any time.
Performance Analytics: Turn Data into Action
Harness the power of your maintenance data. MaintWiz’s robust analytics tools transform raw data into actionable insights, helping you identify trends, optimize strategies, and drive continuous improvement in your maintenance operations.
Resource Optimization: Maximize Efficiency, Minimize Waste
Make the most of your maintenance resources. Our intelligent system helps you allocate manpower, manage inventory, and schedule tasks with precision, ensuring optimal resource utilization and significant cost savings.
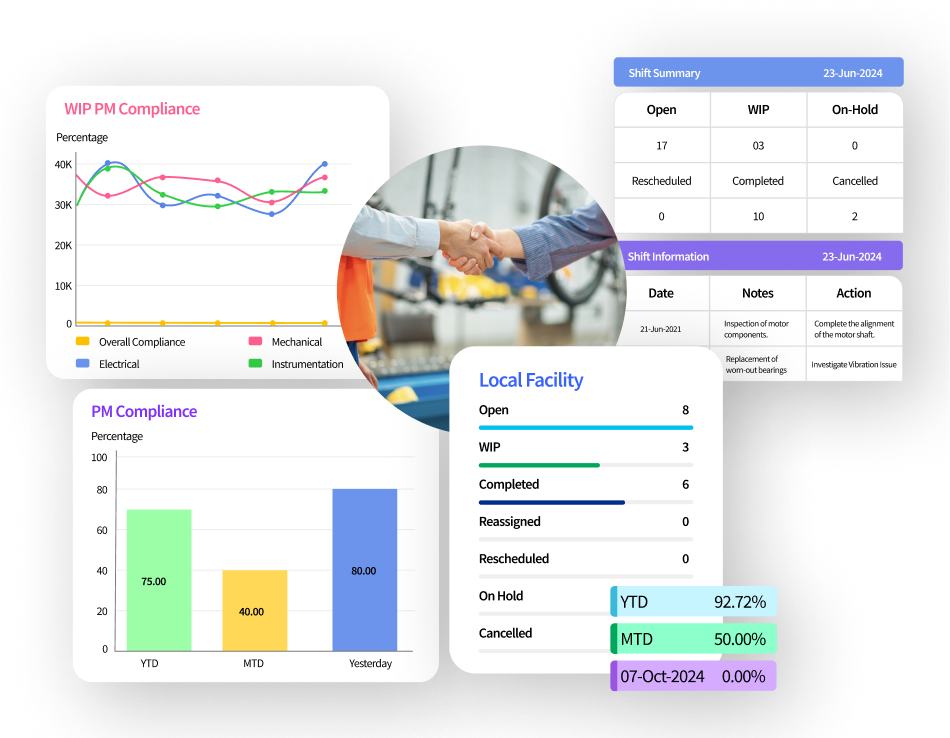
Top Companies in India & Abroad Trust MaintWiz CMMS
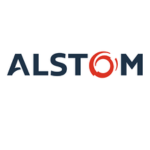
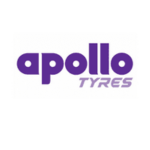
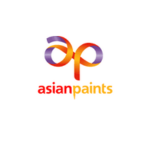
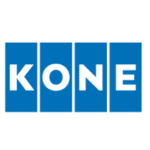
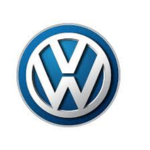
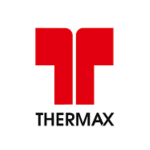
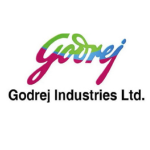
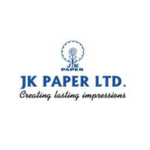
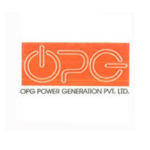
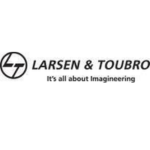
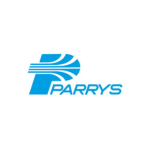
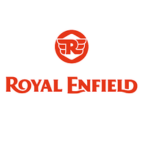
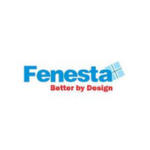
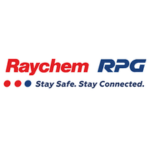
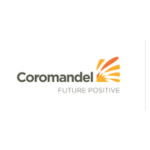
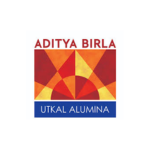
Advanced Planning and Strategy: Blueprint for Maintenance Excellence
Elevate your maintenance planning to new heights with MaintWiz CMMS. Our advanced tools and AI-driven insights enable you to craft strategies that anticipate needs, mitigate risks, and drive operational excellence.
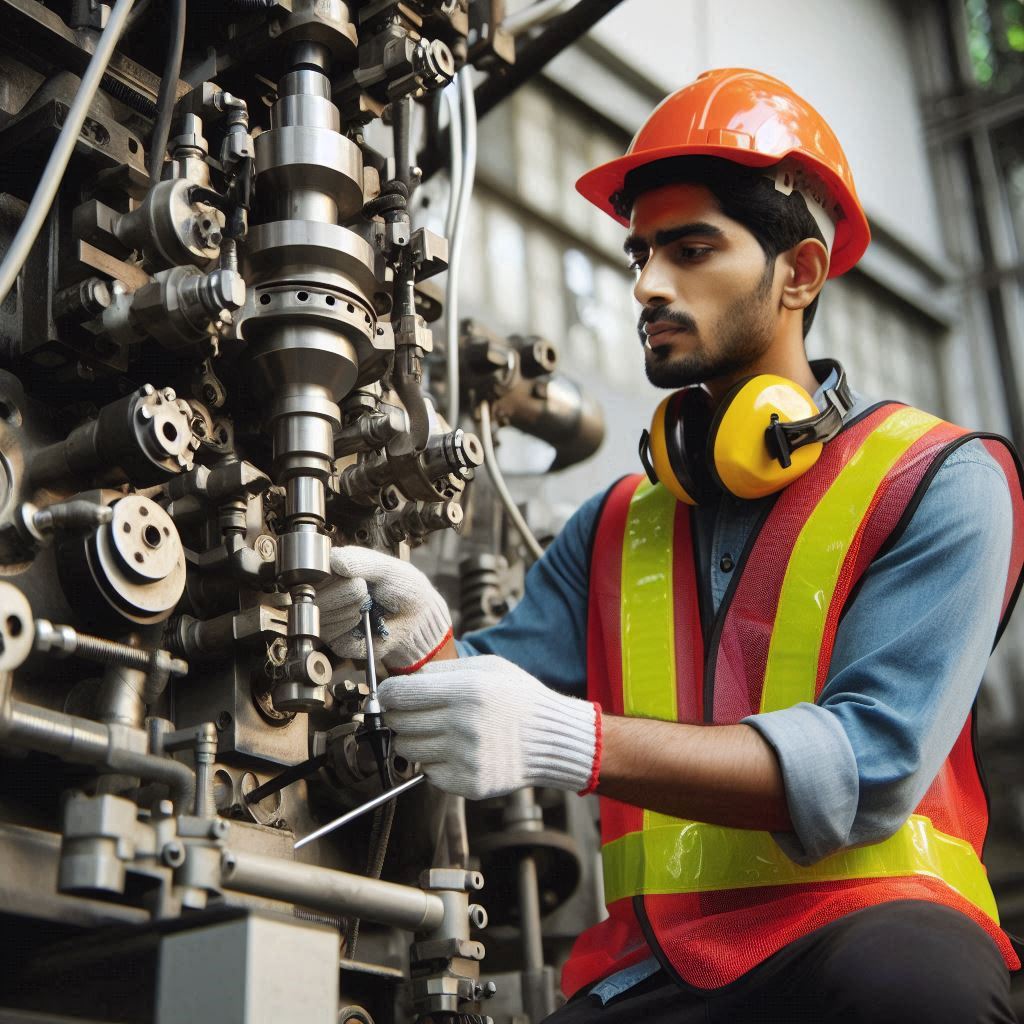
Risk-Based Maintenance Prioritization: Focus on What Matters Most
Not all assets are created equal. MaintWiz’s risk assessment tools help you identify critical assets and prioritize maintenance activities, ensuring your resources are allocated where they’ll have the greatest impact on reliability and performance.
Predictive Maintenance Integration: Stay Ahead of Breakdowns
Combine the power of preventive and predictive maintenance. Our system integrates advanced analytics and machine learning to forecast potential failures, allowing you to address issues before they impact your operations.
Continuous Improvement Framework: Ever-Evolving Excellence
Maintenance strategies should never stand still. MaintWiz provides a robust framework for continuous improvement, helping you analyze outcomes, identify best practices, and refine your approach for ever-increasing efficiency.
Compliance Management: Stay Ahead of Regulatory Requirements
Navigate the complex world of maintenance compliance with ease. Our platform helps you track regulatory requirements, schedule necessary inspections, and maintain thorough documentation to ensure you’re always audit-ready.
Energy Efficiency Planning: Maintain Assets, Reduce Footprint
Align your maintenance strategy with sustainability goals. MaintWiz helps you identify opportunities to improve energy efficiency through targeted maintenance, contributing to both cost savings and environmental stewardship.
Scenario Planning Tools: Prepare for Every Possibility
In maintenance, preparation is key. Our scenario planning tools allow you to model different maintenance strategies, helping you make informed decisions and ensure your team is ready to tackle any challenge that comes your way.
Our Benefits
Efficient Task Management: Streamlined Operations for Peak Performance
Transform your maintenance workflow with MaintWiz CMMS. Our comprehensive task management system ensures smooth execution of preventive maintenance activities, boosting productivity and minimizing downtime.
Intelligent Work Order Generation: Automation that Drives Efficiency
Say goodbye to manual work order creation. MaintWiz automatically generates detailed work orders based on your preventive maintenance schedules, ensuring no task is overlooked and your team always knows what needs to be done.
Dynamic Task Prioritization: Focus on What's Critical
Not all tasks are created equal. Our system intelligently prioritizes maintenance activities based on asset criticality, operational impact, and resource availability, ensuring your team always tackles the most important tasks first.
Collaborative Maintenance Ecosystem: Teamwork Makes the Dream Work
Break down silos in your maintenance operations. MaintWiz fosters collaboration between technicians, supervisors, and management, enabling real-time communication, knowledge sharing, and swift problem resolution.
Skill-Based Assignment: Right Person, Right Job, Right Time
Maximize your team’s potential. Our platform matches tasks with technician skills and certifications, ensuring the right person is always assigned to the job, improving efficiency and quality of maintenance work.
Digital Checklists and Procedures: Consistency in Every Task
Standardize your maintenance processes for consistent, high-quality results. MaintWiz’s digital checklists and procedure guides ensure every task is performed correctly, every time, reducing errors and improving asset reliability.
Time and Cost Tracking: Granular Insights for Better Budgeting
Gain visibility into the true cost of maintenance. Our system tracks time and resources spent on each task, providing valuable data for budget planning, resource allocation, and identifying opportunities for efficiency improvements.
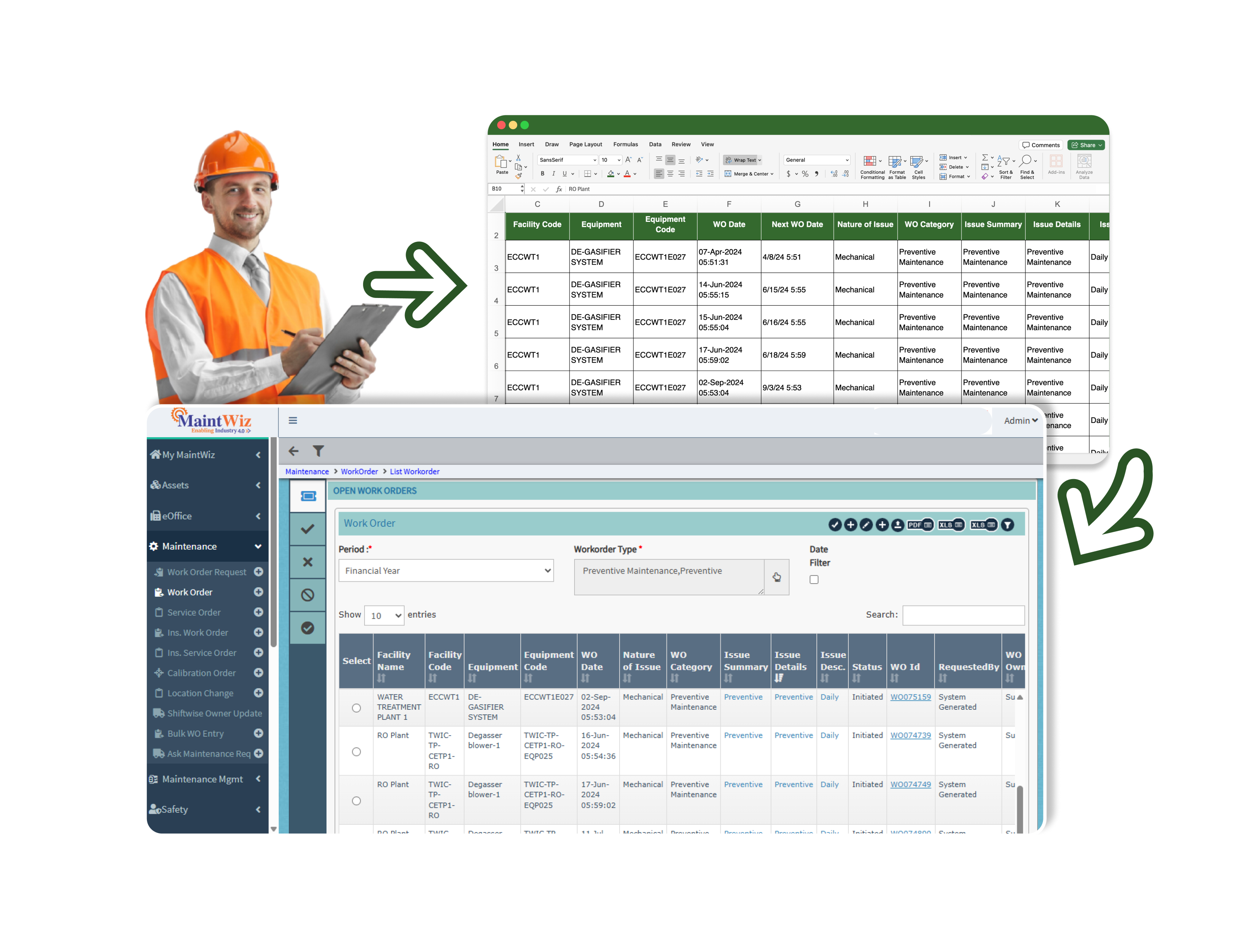
Voices of Our Valued Clients
Comprehensive Reporting and Analytics: Data-Driven Decisions for Maintenance Excellence
Unlock the full potential of your maintenance data with MaintWiz CMMS. Our powerful reporting and analytics tools transform raw data into actionable insights, empowering you to make informed decisions and drive continuous improvement.
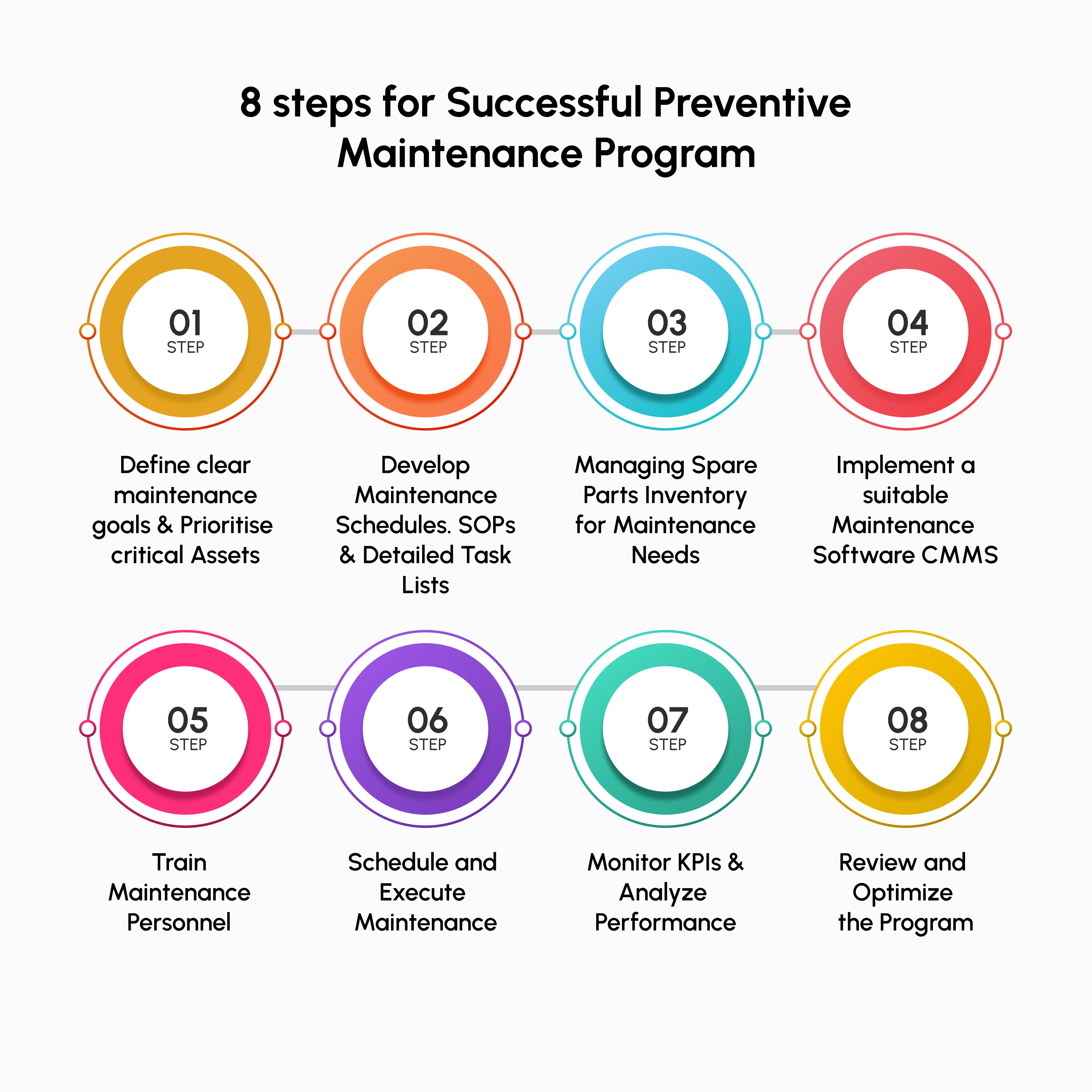
Customizable Dashboard: Your Maintenance Command Center
Get a bird’s-eye view of your maintenance operations. MaintWiz’s customizable dashboards provide real-time visibility into key performance indicators, allowing you to monitor asset health, track maintenance progress, and identify areas for improvement at a glance.
Predictive Analytics: Foresight for Proactive Maintenance
Stay one step ahead of equipment failures. Our advanced predictive analytics leverage historical data and machine learning algorithms to forecast potential issues, enabling you to address problems before they impact your operations.
Cost-Benefit Analysis Tools: Maximize Your Maintenance ROI
Make informed decisions about your maintenance investments. MaintWiz provides robust cost-benefit analysis tools, helping you evaluate the effectiveness of your preventive maintenance strategies and optimize your maintenance budget allocation.
Compliance Reporting: Simplify Audits and Regulatory Requirements
Take the stress out of compliance reporting. Our system automatically generates comprehensive reports for regulatory compliance, making audits a breeze and ensuring you’re always prepared for inspections.
Trend Analysis: Uncover Patterns for Continuous Improvement
Identify opportunities for enhancement in your maintenance practices. MaintWiz’s trend analysis tools help you spot recurring issues, evaluate the effectiveness of your strategies over time, and make data-driven decisions for ongoing optimization.
Asset Lifecycle Analysis: Inform Strategic Asset Management
Explore our Complete Asset Management Solution
Discover the power of a comprehensive asset management solution designed to optimize your operations, extend asset lifecycles, and reduce costs. From real-time tracking to predictive maintenance, our solution empowers your team to make data-driven decisions that enhance efficiency and ensure long-term sustainability.
Breakdown Maintenance
Minimize downtime with fast, reliable response to unexpected equipment failures.
Asset Intelligence
Utilize AI-driven insights to make smarter decisions on asset maintenance and performance.
Internet of Things (IoT)
Leverage IoT technology to gather real-time data for smarter maintenance decisions.
Work Order Management
Simplify work orders to enhance maintenance workflows and productivity.
Digital Twin Technology
Simulate asset performance and maintenance scenarios using digital twin technology.
Energy Management
Reduce energy consumption and costs by optimizing asset energy efficiency.
Condition Monitoring
Monitor equipment conditions in real-time to predict potential failures.
Maintenance Budgeting
Effectively manage and control your maintenance budget to maximize ROI.
Request a one-one demo with our solution engineering team.
Request a one-one demo with our solution engineering team.
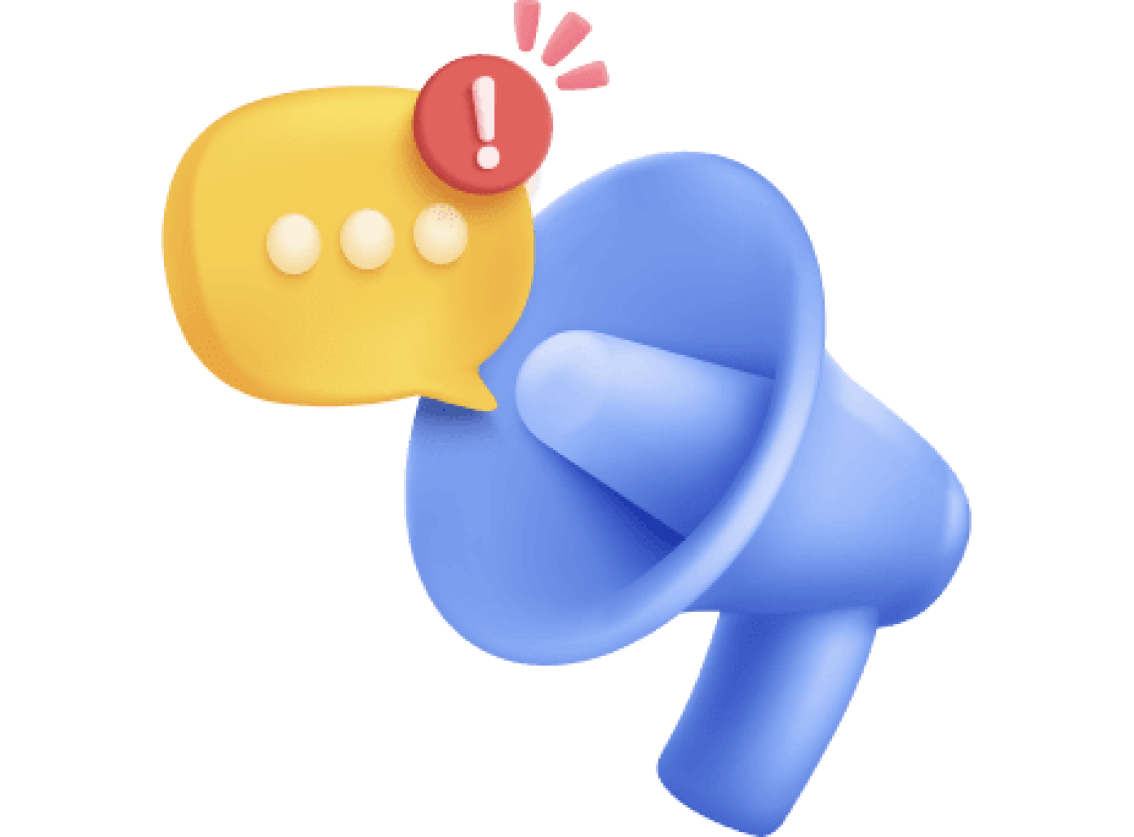
MaintWiz revolutionized our preventive maintenance approach, cutting unplanned downtime by over 35% annually.