How to Improve Your
OEE with TPM
How to Improve Your OEE with TPM
Table of Contents
ToggleHow to Improve Your OEE with TPM
1. Introduction to OEE and TPM
In the world of manufacturing, optimizing productivity and efficiency is crucial. Understanding how Overall Equipment Effectiveness (OEE) and Total Productive Maintenance (TPM) can work together is essential to achieve manufacturing excellence.
Definition and Explanation of OEE and TPM
OEE is a performance metric that measures the effectiveness of equipment utilization in a manufacturing process. TPM, on the other hand, is a holistic approach to maintenance that aims to maximize equipment reliability, minimize downtime, and optimize maintenance effectiveness. Combining OEE and TPM allows organizations to achieve higher levels of operational efficiency and performance.
Importance of OEE and TPM in Manufacturing
OEE and TPM play vital roles in manufacturing. OEE provides insights into equipment utilization and identifies areas for improvement, while TPM focuses on proactive maintenance practices to ensure equipment reliability. By integrating OEE and TPM, organizations can enhance productivity, reduce downtime, and improve overall equipment performance.
Benefits of Combining OEE and TPM
By combining OEE and TPM, organizations can experience a range of benefits, including:
- Increased equipment uptime and availability
- Improved equipment efficiency and performance
- Enhanced product quality and reduced defects
- Minimized unplanned downtime and maintenance costs
- Greater employee engagement and ownership in maintenance activities
- Continuous improvement culture for sustained operational excellence
2. Understanding Total Productive Maintenance (TPM)
Total Productive Maintenance (TPM) is a comprehensive approach to equipment maintenance that focuses on maximizing overall equipment effectiveness through employee involvement, standardized processes, and proactive maintenance practices.
Definition and Principles of TPM
TPM is based on the principles of:
- Employee involvement and empowerment
- Preventive and proactive maintenance practices
- Equipment reliability and availability
- Continuous improvement and zero losses
Pillars of TPM Implementation
The implementation of TPM is supported by several key pillars, including:
- Autonomous Maintenance: Empowering operators to perform routine equipment maintenance tasks
- Planned Maintenance: Scheduled maintenance activities based on equipment condition and performance
- Focused Improvement: Identifying and addressing root causes of equipment losses and inefficiencies
- Education and Training: Providing employees with the necessary skills and knowledge for effective maintenance
- Quality Maintenance: Ensuring equipment reliability and performance through quality control measures
- Early Equipment Management: Involving equipment designers and users in improving equipment reliability
- Safety, Health, and Environment: Integrating safety and environmental considerations into maintenance practices
Role of TPM in Equipment Reliability and Maintenance Effectiveness
TPM aims to improve equipment reliability, minimize downtime, and enhance maintenance effectiveness. By implementing TPM practices, organizations can:
- Reduce equipment failures and breakdowns
- Increase equipment uptime and availability
- Optimize maintenance activities and resource allocation
- Improve equipment performance and efficiency
- Enhance overall equipment reliability and lifespan
3. OEE and TPM: A Powerful Combination
OEE and TPM are complementary methodologies that, when combined, create a powerful approach to maximize equipment performance and achieve manufacturing excellence.
Relationship between OEE and TPM
OEE and TPM share a common goal of optimizing equipment effectiveness. OEE provides a quantitative measure of equipment utilization, while TPM focuses on the proactive maintenance practices necessary to achieve high levels of equipment reliability and availability. By integrating OEE and TPM, organizations can take a holistic approach to improving equipment performance and overall operational efficiency.
How TPM Can Enhance OEE Performance
TPM enhances OEE performance by:
- Preventing equipment failures through proactive maintenance practices
- Reducing unplanned downtime and equipment breakdowns
- Improving equipment efficiency and performance
- Engaging operators in autonomous maintenance activities
- Ensuring equipment is in optimal condition for maximum productivity
Synergies between OEE and TPM Methodologies
OEE and TPM methodologies share common principles and practices, including:
- Employee involvement and empowerment
- Proactive maintenance and equipment reliability
- Data-driven decision-making for continuous improvement
- Standardization of processes and best practices
4. Assessing OEE and Identifying Improvement Areas
Assessing OEE and identifying areas for improvement are crucial steps in enhancing equipment performance and overall operational efficiency.
OEE Measurement and Calculation Methods
OEE is typically calculated using the formula:
OEE = Availability Ă— Performance Ă— Quality
MaintWiz CMMS simplifies OEE measurement by automatically collecting relevant data, such as equipment downtime, production rates, and product quality. By leveraging the power of MaintWiz CMMS, you can obtain accurate and real-time OEE measurements for your manufacturing processes.
Identifying Major Losses and Bottlenecks in Production
MaintWiz CMMS provides comprehensive insights into production losses and bottlenecks. By analyzing OEE data and utilizing advanced reporting features, you can identify and address major sources of equipment inefficiencies, such as breakdowns, setup and changeover time, and quality defects. This enables targeted improvement efforts to optimize OEE and maximize production output.
Collecting and Analyzing OEE Data for Improvement Insights
MaintWiz CMMS facilitates data collection and analysis for OEE improvement. By capturing equipment performance data, tracking maintenance activities, and correlating this information with OEE metrics, you can gain valuable insights into the root causes of equipment inefficiencies and take proactive measures to enhance OEE.
5. Implementing TPM Practices to Improve OEE
Implementing TPM practices is crucial to improving OEE performance. MaintWiz CMMS offers a range of features and functionalities that support the implementation of TPM strategies.
Establishing Autonomous Maintenance Practices
MaintWiz CMMS empowers operators to take ownership of equipment maintenance through autonomous maintenance practices. By providing operators with the necessary tools and resources, such as work instructions, checklists, and maintenance schedules, MaintWiz CMMS enables them to perform routine maintenance tasks, identify abnormalities, and contribute to the overall equipment reliability and OEE improvement efforts.
Planned Maintenance and Preventive Maintenance Strategies
MaintWiz CMMS facilitates the implementation of planned and preventive maintenance strategies. By automating maintenance scheduling, generating work orders, and tracking maintenance activities, MaintWiz CMMS ensures that equipment maintenance is performed in a timely manner, minimizing the risk of unplanned downtime and optimizing equipment performance.
Focused Improvement Initiatives for Increased Equipment Efficiency
MaintWiz CMMS supports focused improvement initiatives by providing tools for root cause analysis, problem-solving, and continuous improvement projects. With features like failure analysis, trend analysis, and improvement tracking, MaintWiz CMMS enables you to identify improvement opportunities, implement targeted actions, and monitor the effectiveness of your OEE and TPM improvement initiatives.
6. Training and Engagement for OEE Improvement
Training employees on TPM principles and fostering engagement are essential for OEE improvement. MaintWiz CMMS offers capabilities that facilitate training and cross-functional collaboration.
Educating Employees on TPM Principles and Techniques
MaintWiz CMMS provides a centralized platform for sharing knowledge and training materials related to TPM. With document management features and training module integration, MaintWiz CMMS enables organizations to educate employees on TPM principles, best practices, and techniques, fostering a common understanding and alignment towards OEE improvement goals.
Encouraging Operator Involvement and Ownership in Maintenance Activities
MaintWiz CMMS promotes operator involvement and ownership in maintenance activities through its user-friendly interface and mobile accessibility. Operators can easily access work instructions, record equipment observations, and report abnormalities, contributing to the early detection of potential equipment issues and driving proactive maintenance practices for improved OEE.
Continuous Improvement Culture and Cross-Functional Collaboration
MaintWiz CMMS supports the development of a continuous improvement culture by providing collaboration features, such as discussion forums and knowledge sharing platforms. By facilitating cross-functional collaboration and encouraging employees to share ideas and insights, MaintWiz CMMS fosters a culture of continuous learning, innovation, and improvement for sustained OEE gains.
7. OEE and TPM Performance Metrics
Monitoring performance metrics is essential for evaluating the effectiveness of OEE and TPM initiatives. MaintWiz CMMS offers comprehensive performance tracking and reporting capabilities.
Key Performance Indicators (KPIs) for Measuring OEE and TPM Effectiveness
MaintWiz CMMS provides a range of KPIs to measure OEE and TPM effectiveness, including:
- OEE: Overall Equipment Effectiveness
- Availability: Percentage of time equipment is available for production
- Performance: Equipment efficiency and production rate
- Quality: Percentage of products meeting quality standards
- Mean Time Between Failures (MTBF)
- Mean Time to Repair (MTTR)
- Planned vs. Unplanned Maintenance Ratio
- First Pass Yield (FPY)
Setting Performance Targets and Monitoring Progress
MaintWiz CMMS allows you to set performance targets for OEE and TPM metrics and track progress towards achieving those targets. With customizable dashboards and real-time reporting, MaintWiz CMMS provides visibility into performance trends, deviations, and areas requiring improvement, enabling you to take timely actions to optimize OEE performance.
Visual Management and Performance Dashboards for Real-Time Tracking
MaintWiz CMMS offers visual management tools, such as performance dashboards and real-time equipment status displays. These features allow you to monitor OEE and TPM performance at a glance, quickly identify areas of concern, and make data-driven decisions for continuous improvement.
8. Case Studies: OEE Improvement through TPM
Real-life examples demonstrate the effectiveness of TPM in improving OEE. Explore these case studies that highlight the diverse industries and the quantifiable benefits achieved through TPM-driven OEE improvement.
Case Study 1: Automotive Industry
In the automotive industry, a leading manufacturer implemented TPM practices to improve OEE. By focusing on autonomous maintenance, planned maintenance, and equipment reliability initiatives, they achieved a 15% increase in OEE, reduced unplanned downtime by 30%, and improved overall production efficiency.
Case Study 2: Food and Beverage Industry
A food and beverage company adopted TPM methodologies to enhance OEE in their production lines. Through operator training, focused improvement projects, and quality maintenance initiatives, they achieved a 20% reduction in equipment failures, a 25% increase in equipment availability, and a significant improvement in product quality and customer satisfaction.
Case Study 3: Pharmaceutical Industry
A pharmaceutical manufacturer implemented TPM strategies to optimize OEE and comply with stringent regulatory requirements. By implementing standardized maintenance practices, improving changeover efficiency, and leveraging digital technologies, they achieved a 10% increase in OEE, reduced changeover time by 50%, and ensured compliance with regulatory standards.
Case Study 4: Electronics Industry
An electronics manufacturer implemented TPM practices to enhance OEE and reduce production costs. Through focused improvement projects, equipment reliability initiatives, and cross-functional collaboration, they achieved a 12% increase in OEE, reduced maintenance costs by 20%, and improved overall equipment performance and product quality.
Case Study 5: Chemical Industry
A chemical plant implemented TPM methodologies to optimize OEE and minimize equipment failures. By implementing autonomous maintenance practices, improving equipment changeover efficiency, and establishing preventive maintenance strategies, they achieved a 25% reduction in equipment breakdowns, a 30% increase in equipment availability, and enhanced operational stability and safety.
Case Study 6: Metal Manufacturing Industry
A metal manufacturer implemented TPM initiatives to improve OEE and reduce production waste. Through focused improvement projects, operator engagement, and continuous improvement culture, they achieved a 15% increase in OEE, reduced scrap and rework by 20%, and improved overall equipment effectiveness and production efficiency.
Case Study 7: Packaging Industry
A packaging company implemented TPM practices to optimize OEE and increase production capacity. By implementing planned maintenance strategies, operator skill development programs, and equipment reliability initiatives, they achieved a 20% increase in OEE, reduced changeover time by 40%, and improved overall equipment performance and efficiency.
Challenges Faced and Lessons Learned During TPM Implementation
While implementing TPM, organizations may face challenges such as resistance to change, lack of employee engagement, and the need for cultural transformation.
It is crucial to address these challenges by providing adequate training, fostering a supportive environment, and promoting a continuous improvement mindset. MaintWiz CMMS can support organizations in overcoming these challenges and learning from the experiences of others.
Quantifiable Benefits and ROI Achieved with TPM-Driven OEE Improvement
The quantifiable benefits of TPM-driven OEE improvement include:
- Increased equipment uptime and availability
- Reduced unplanned downtime and production losses
- Improved equipment efficiency and performance
- Enhanced product quality and customer satisfaction
- Optimized maintenance resources and reduced costs
- Higher return on investment (ROI) and improved profitability
9. Continuous Improvement and Sustaining OEE Gains
Continuous improvement is essential for sustaining OEE gains and achieving long-term operational excellence. MaintWiz CMMS supports organizations in their continuous improvement journey.
PDCA (Plan-Do-Check-Act) Cycle for Ongoing Improvement
The PDCA cycle is a systematic approach to continuous improvement. MaintWiz CMMS helps organizations implement the PDCA cycle by providing tools for planning improvement actions, executing them, checking the results, and taking necessary corrective actions. This iterative process ensures ongoing improvement and sustained OEE gains.
Management Review and Performance Feedback Loops
MaintWiz CMMS facilitates management reviews and performance feedback loops. By providing performance reports, metrics tracking, and data visualization, MaintWiz CMMS enables management to review progress, identify areas for further improvement, and provide feedback to drive continuous OEE enhancement initiatives.
Sustaining OEE Gains through Continuous Training and Reinforcement
MaintWiz CMMS supports continuous training and reinforcement of TPM and OEE improvement principles. By providing training modules, knowledge sharing platforms, and performance tracking, MaintWiz CMMS ensures that employees stay engaged, knowledgeable, and aligned with the organization’s OEE improvement goals.
10. Future Trends and Innovations in TPM and OEE
The future of TPM and OEE is driven by emerging technologies and industry trends. MaintWiz CMMS keeps organizations at the forefront of these innovations.
Integration of Digital Technologies in TPM Practices
MaintWiz CMMS integrates with digital technologies, such as the Internet of Things (IoT), artificial intelligence (AI), and machine learning (ML), to enable predictive maintenance, remote monitoring, and advanced analytics. By harnessing these technologies, organizations can optimize equipment performance, anticipate maintenance needs, and achieve higher levels of OEE.
Predictive and Prescriptive Maintenance for Enhanced OEE
MaintWiz CMMS supports predictive and prescriptive maintenance strategies. By leveraging historical data, equipment condition monitoring, and AI-based algorithms, MaintWiz CMMS can predict potential equipment failures, prescribe maintenance actions, and optimize maintenance schedules. This proactive approach minimizes downtime, maximizes equipment reliability, and improves OEE performance.
Industry 4.0 and the Role of TPM in Smart Manufacturing Systems
Industry 4.0 revolutionizes manufacturing through the integration of advanced technologies, such as IoT, cloud computing, and data analytics. MaintWiz CMMS aligns with the principles of Industry 4.0 by providing a digital platform for smart manufacturing, where TPM practices, OEE improvement, and data-driven decision-making converge. MaintWiz CMMS enables organizations to embrace the benefits of Industry 4.0 and unlock new opportunities for OEE optimization and operational excellence.
Conclusion
In conclusion, improving your OEE with TPM is a powerful strategy for achieving manufacturing excellence. By leveraging MaintWiz CMMS, you can unlock the full potential of OEE and TPM, optimize equipment performance, reduce downtime, and drive continuous improvement. Take the first step towards enhancing your OEE by implementing TPM practices with MaintWiz CMMS today.
Key Takeaways:
- OEE and TPM are essential for achieving manufacturing excellence.
- Combining OEE and TPM leads to increased equipment uptime, improved efficiency, and enhanced product quality.
- TPM principles include employee involvement, proactive maintenance, and continuous improvement.
- OEE measurement methods and data analysis help identify improvement areas.
- Implementing TPM practices, such as autonomous maintenance and planned maintenance, improves OEE performance.
- Training and engagement foster operator involvement in maintenance activities and create a continuous improvement culture.
- Monitoring TPM and OEE performance metrics allows for tracking progress and setting targets.
- Real-life case studies demonstrate the effectiveness of TPM in various industries.
- Continuous improvement and sustaining OEE gains require the PDCA cycle and management review.
- Future trends include the integration of digital technologies, predictive maintenance, and Industry 4.0.
Request a one-one demo with our solution engineering team.
Request a one-one demo with our solution engineering team.
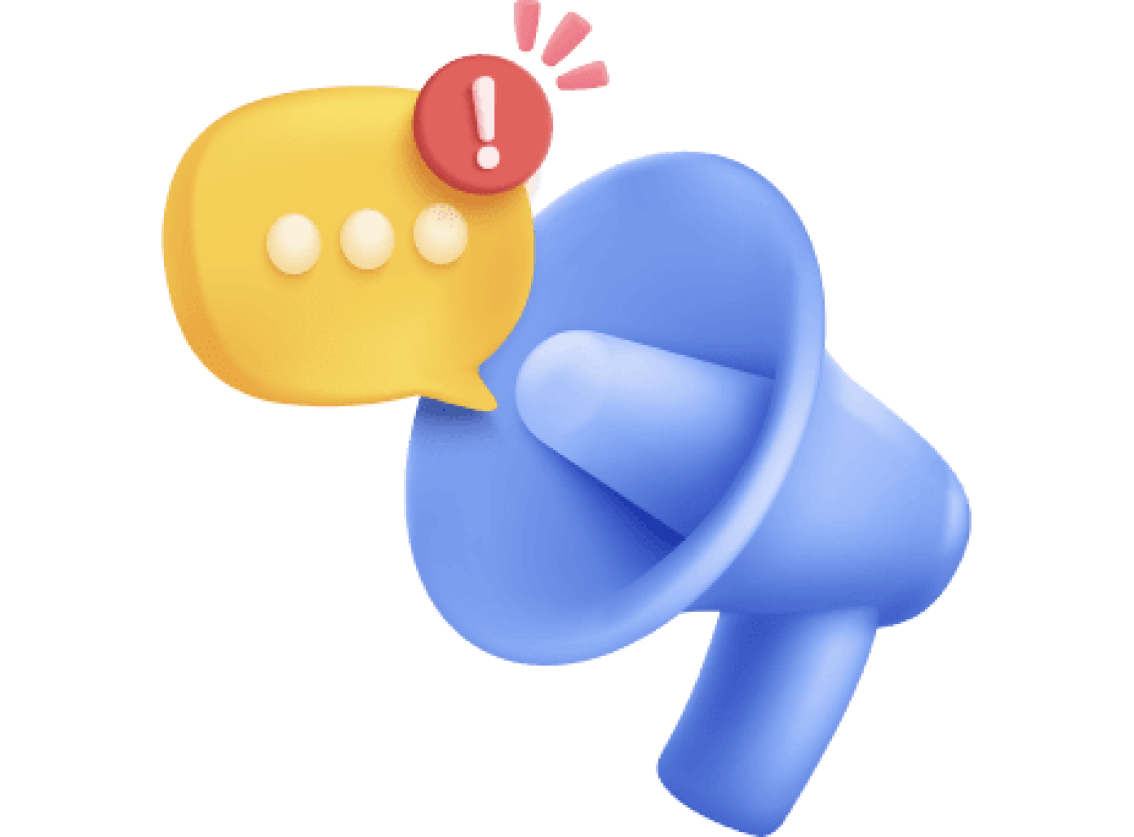