Transform Industrial Operations with Enterprise-Grade Connected Systems
Revolutionize your operational excellence through seamless integration of IT and OT infrastructure. MaintWiz CMMS delivers real-time visibility, AI-driven insights, and unified control across your entire industrial technology ecosystem.
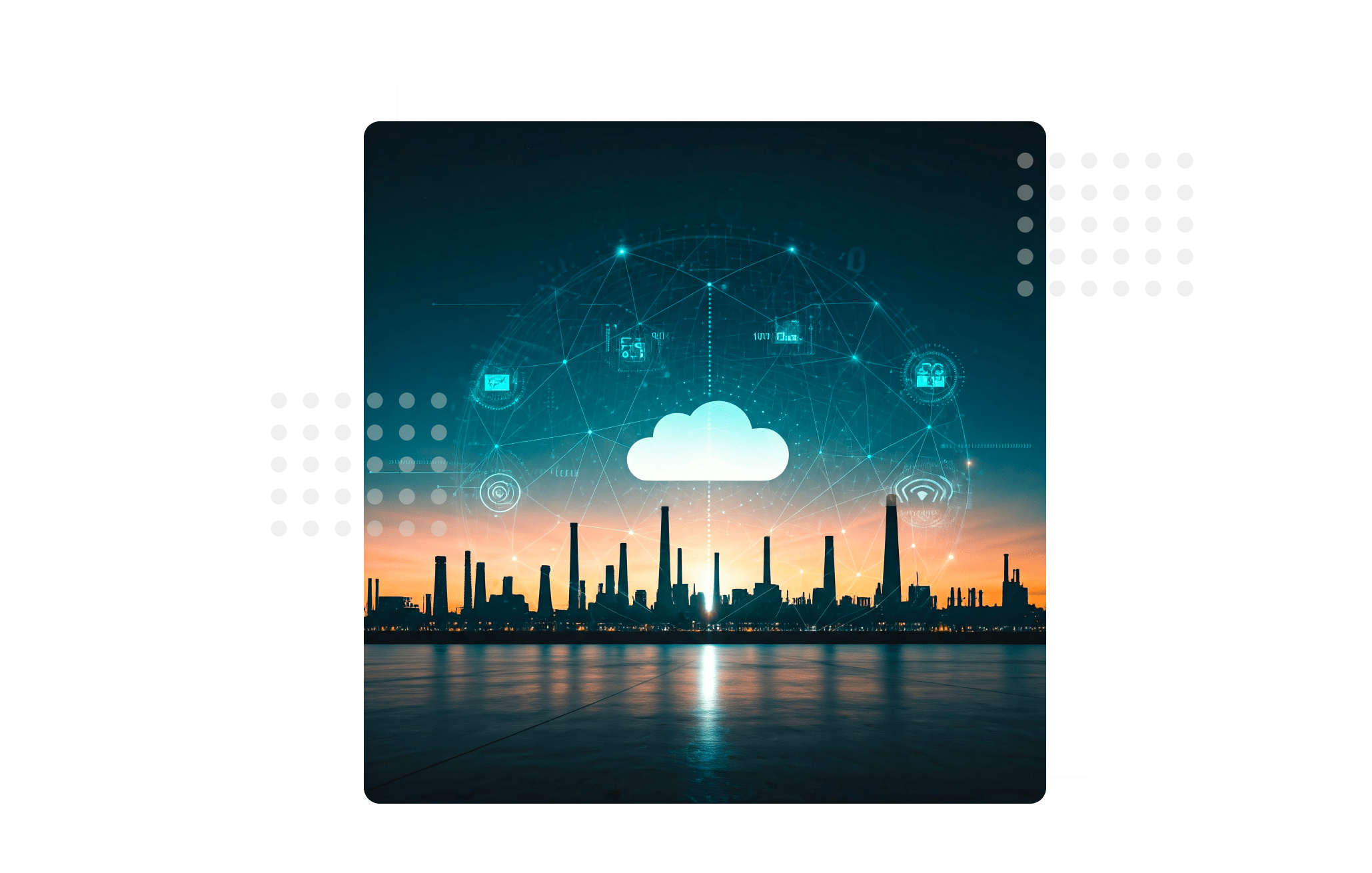
Redefine Asset Management Through Intelligent System Integration
MaintWiz's Smart Workforce CMMS platform represents the future of maintenance management, seamlessly integrating artificial intelligence with intuitive workflows to transform traditional maintenance operations into data-driven, efficient processes. Our innovative solution empowers maintenance teams with real-time insights, predictive capabilities, and collaborative tools, ensuring maximum asset uptime while optimizing operational costs and resource utilization.
Enterprise Technology Integration Hub
Unify your entire technology stack through MaintWiz's intelligent integration capabilities, enabling seamless communication between enterprise systems and operational technologies.
Centralized Command Center for Enterprise Applications
Execute strategic control over your digital infrastructure through a unified platform that streamlines operations, reduces redundancy, and enables real-time decision making across integrated systems.
Seamless Enterprise Technology Orchestration
Deploy advanced APIs and connectors to create a harmonious flow of information between critical business systems, ensuring data consistency and enabling automated workflows across your organization.
IT-OT Convergence Framework
Bridge the gap between information technology and operational technology systems with our sophisticated integration framework, enabling comprehensive visibility and control over your entire operational ecosystem.
Enterprise-Wide Data Governance
Implement robust data management protocols across integrated systems, ensuring data quality, compliance, and security while enabling authorized access to critical operational information.
Automated Cross-System Updates
Eliminate manual data entry and reduce errors through automated synchronization of critical information across integrated platforms, ensuring consistency and reliability in your operations.
Cloud-Enabled Remote Operations
Access your integrated systems from anywhere through secure cloud connectivity, enabling remote monitoring, control, and decision-making capabilities for distributed teams.
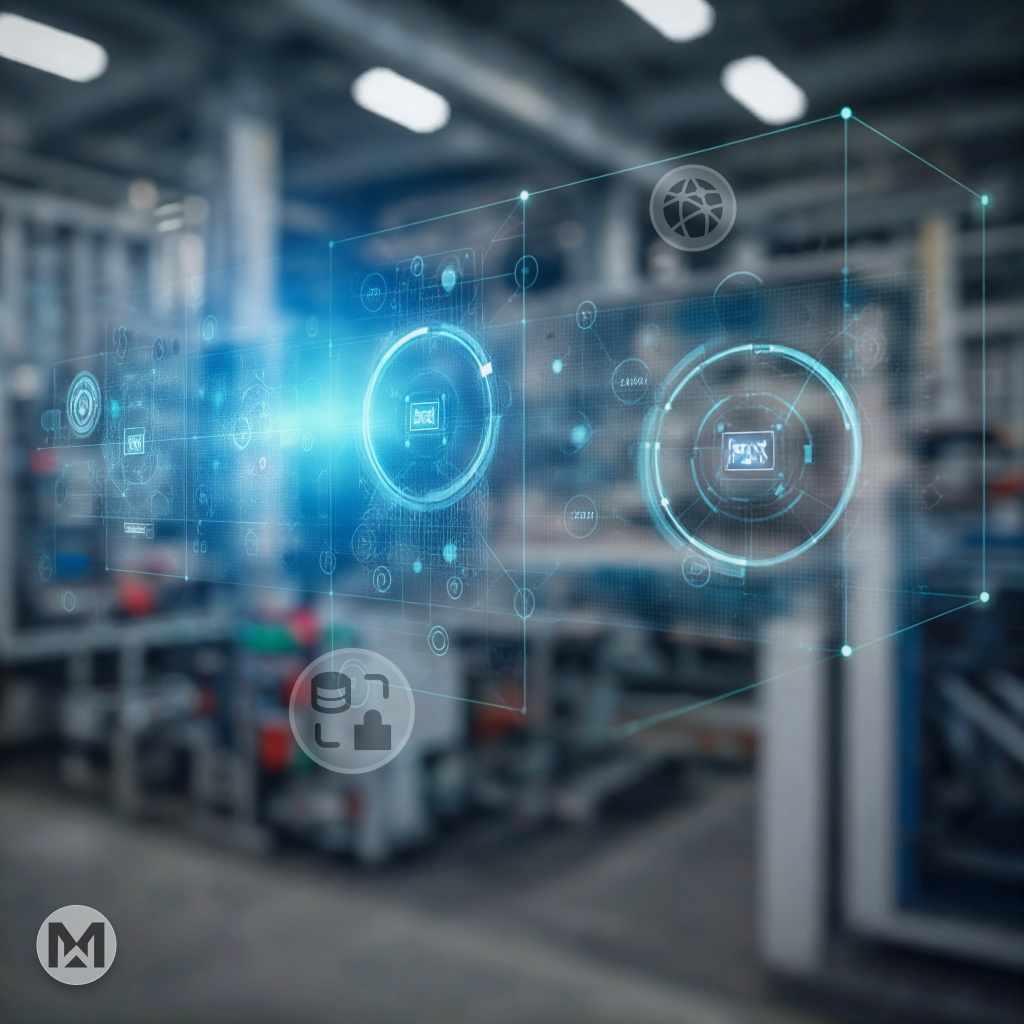
Smart Operational Technology Integration
Transform operational efficiency by connecting industrial assets directly to your maintenance management system through intelligent OT integration capabilities
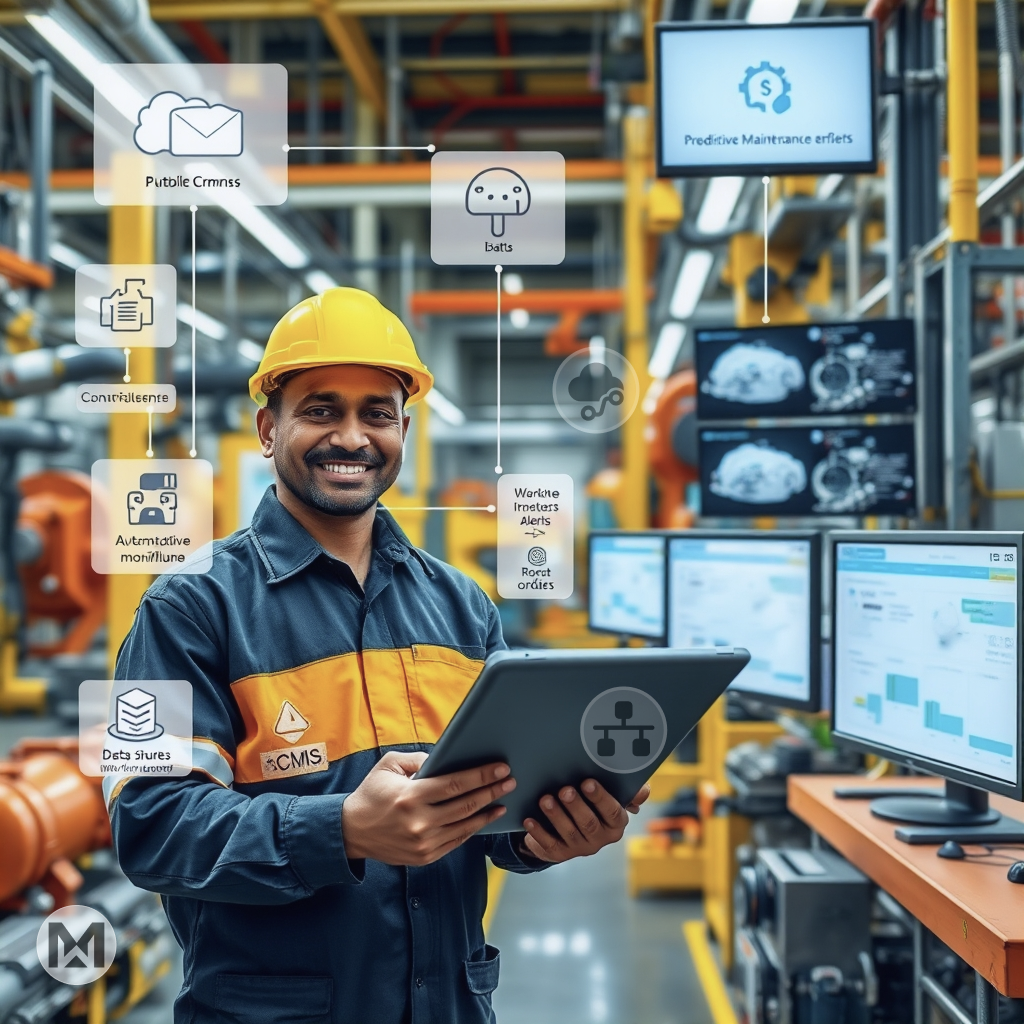
Real-Time OT Data Integration
Connect industrial assets directly to your maintenance system through advanced IoT protocols, enabling immediate access to operational data and facilitating proactive maintenance decisions.
Predictive Analytics Engine
Leverage machine learning algorithms to analyze operational data streams, identifying potential issues before they impact production and optimizing maintenance schedules based on actual asset condition.
IoT Sensor Network Management
Deploy and manage comprehensive sensor networks across your facility, collecting real-time data on equipment performance, environmental conditions, and operational parameters.
Automated Alert Intelligence
Configure smart alerts based on real-time operational data, enabling immediate response to critical situations and ensuring optimal asset performance through proactive maintenance.
Comprehensive Process Visualization
Gain unprecedented visibility into your operational processes through intuitive dashboards that display real-time asset performance metrics and operational KPIs.
Dynamic Equipment Health Monitoring
Monitor equipment health in real-time through advanced diagnostics and performance analytics, enabling immediate response to potential issues and optimizing maintenance activities.
Speak to a Specialist
Get personalised advice from our experts
Enterprise-Wide Data Synchronization
Enable seamless data flow between your critical business systems with MaintWiz's advanced synchronization capabilities, ensuring real-time accuracy across your entire operation.
Bidirectional ERP Integration
Establish seamless two-way communication between your CMMS and ERP systems, ensuring critical business data remains synchronized and enabling more informed decision-making processes.
Real-Time SCADA Data Integration
Connect your SCADA systems directly to MaintWiz CMMS, enabling real-time monitoring of industrial processes and immediate response to operational changes or potential issues.
Automated Schedule Synchronization
Maintain perfect alignment between maintenance schedules and production plans through automated synchronization, optimizing resource utilization and minimizing operational disruptions.
Centralized Data Repository
Create a single source of truth for all operational data, enabling comprehensive analytics and ensuring consistency across all integrated systems and departments.
Web Services Integration Framework
Leverage modern web services architecture to ensure seamless communication between different systems, regardless of platform or technology stack.
Cross-Platform Data Validation
Implement automated data validation protocols across all integrated systems, ensuring data integrity and reducing the risk of errors in critical business operations.
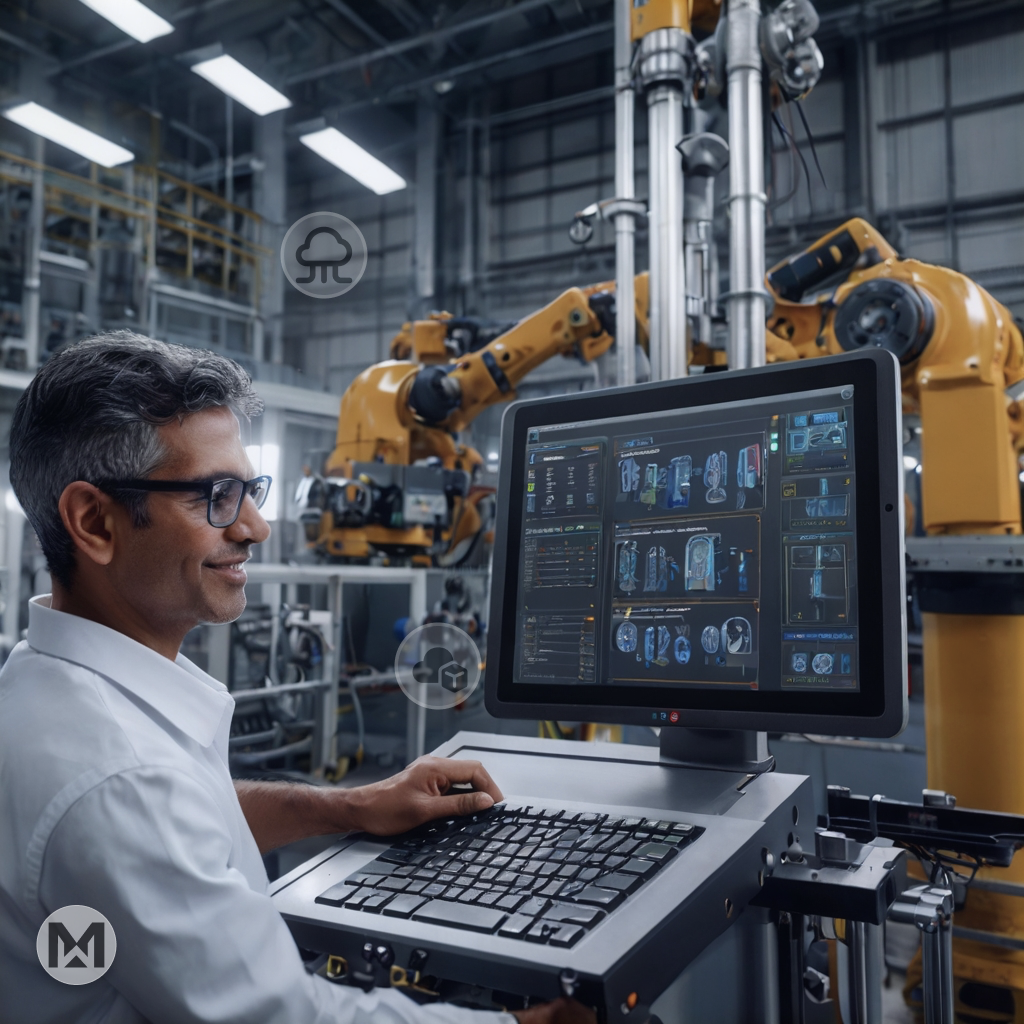
AI-Powered Operational Intelligence
Harness the power of artificial intelligence to transform raw data into actionable insights, enabling predictive maintenance and optimized decision-making across your enterprise.

Unified Data Analytics Platform
Access comprehensive analytics from multiple data sources through a single interface, enabling deeper insights into operational performance and maintenance requirements.
Predictive Maintenance Intelligence
Leverage advanced AI algorithms to predict equipment failures before they occur, optimizing maintenance schedules and reducing unplanned downtime across your operation.
Cross-System Performance Analysis
Analyze performance data across different systems and equipment types, identifying patterns and trends that impact operational efficiency and maintenance requirements.
Automated Decision Support
Receive AI-driven recommendations for maintenance actions, resource allocation, and operational adjustments based on real-time data analysis and historical patterns.
KPI Visualization Dashboard
Monitor critical performance indicators through intuitive dashboards that provide real-time visibility into operational efficiency, maintenance effectiveness, and equipment reliability.
Machine Learning Optimization
Continuously improve maintenance strategies through machine learning algorithms that adapt to your specific operational patterns and equipment behavior.
Cross-Functional Collaboration Platform
Break down departmental silos and enable seamless communication across your organization with MaintWiz's collaborative maintenance management capabilities.
Role-Based Information Access
Control system access and information sharing through customizable role-based permissions, ensuring secure and appropriate access to maintenance and operational data.
Mobile Workforce Enablement
Empower field technicians and operators with mobile access to critical information and work orders, enabling faster response times and improved maintenance execution.
Real-Time Communication Hub
Facilitate instant communication between maintenance teams, operators, and management through integrated messaging and notification systems.
Automated Stakeholder Updates
Keep all stakeholders informed through automated notifications and status updates, ensuring alignment across departments and reducing communication gaps.
Collaborative Work Planning
Enable cross-departmental coordination for maintenance activities through shared calendars, resource allocation tools, and collaborative scheduling features.
Performance Feedback Loop
Create continuous improvement cycles through integrated feedback mechanisms that capture insights from maintenance activities and operational performance.
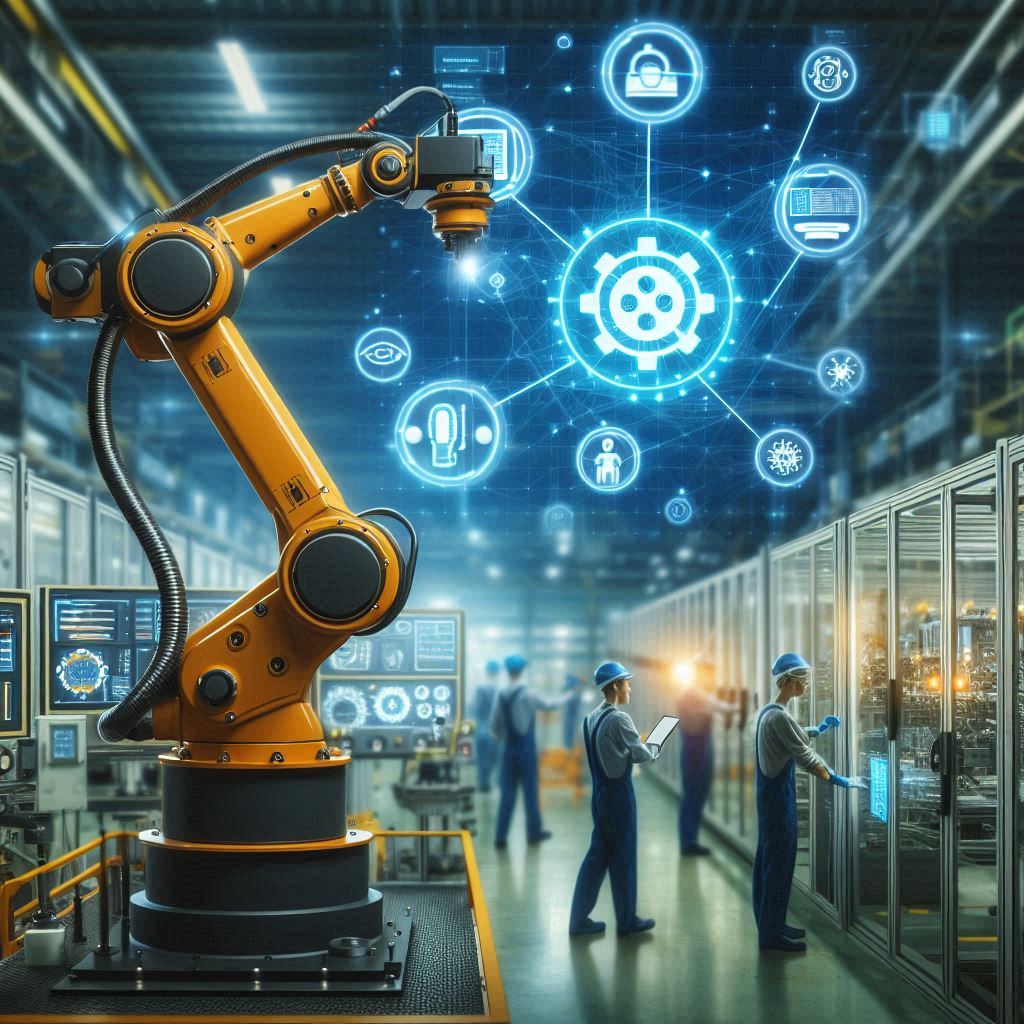
Maximize Asset Intelligence Through IoT Connectivity
Harness the power of connected assets to revolutionize your maintenance strategy with real-time monitoring and intelligent insights.
Advanced Real-Time Asset Health Monitoring System
Transform maintenance decisions with continuous performance tracking & instant health status updates, enabling proactive intervention before issues escalate into costly downtime scenarios.
Enterprise-Wide IoT Integration Framework
Unite all asset data streams into a centralized platform, creating a comprehensive single source of truth that drives informed decision-making and strategic maintenance planning.
Intelligent Pattern Recognition Analytics
Leverage sophisticated algorithms to analyze operational patterns & wear indicators, automatically identifying potential issues & optimization opportunities across your asset portfolio.
Predictive Alert Intelligence System
Deploy smart monitoring algorithms that detect subtle changes in asset behavior, triggering automated alerts before minor issues develop into major failures.
Request a one-one demo with our solution engineering team.
Request a one-one demo with our solution engineering team.