Transform Industrial Asset Management with AI-Powered Digital Foundation
Revolutionize your asset management strategy with MaintWiz’s intelligent CMMS platform. Harness the power of AI and advanced analytics to maximize asset performance, reduce downtime, and drive operational excellence
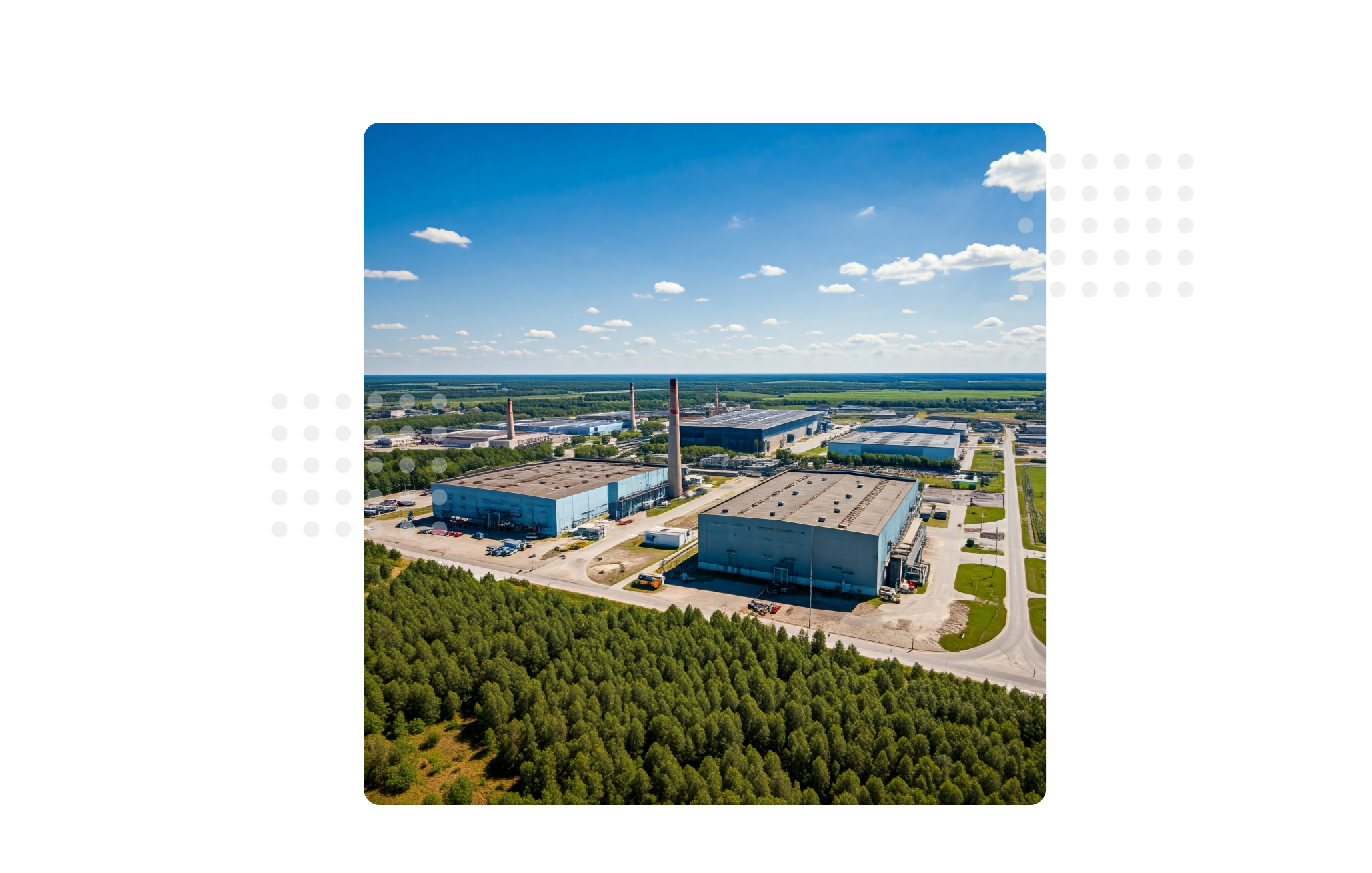
Revolutionize Maintenance Strategy with Industry 4.0 Asset Management
As industrial assets become increasingly complex, traditional maintenance approaches fall short. MaintWiz empowers manufacturers with a comprehensive digital foundation that turns maintenance challenges into competitive advantages. Our intelligent CMMS platform combines real-time monitoring, predictive analytics, and automated workflows to create a proactive maintenance ecosystem. Discover why global leaders trust MaintWiz to deliver 50% faster response times, 35% reduced maintenance costs, and 99.9% asset availability.
Empower Asset Excellence with Unified Digital Infrastructure
Build a robust digital foundation that transforms complex asset data into actionable insights. MaintWiz's enterprise-grade CMMS creates a single source of truth for your entire asset portfolio.
Centralized Asset Intelligence Hub for Enhanced Visibility
Transform asset management with our centralized digital repository, enabling real-time access to critical asset information, maintenance histories, and performance metrics across your enterprise, driving informed decision-making and operational efficiency.
Dynamic Asset Hierarchy Mapping for Global Operations
Implement standardized asset hierarchies that scale across multiple sites, providing clear visualization of asset relationships and dependencies while enabling efficient multi-facility management and maintenance coordination.
Comprehensive Digital Asset Lifecycle Management
Track and optimize every phase of your assets’ lifecycle with detailed digital records, from procurement to retirement, ensuring maximum ROI and strategic resource allocation while maintaining complete audit trails.
Intelligent Location Tracking and Geospatial Analytics
Leverage advanced geolocation capabilities to monitor asset movements, optimize deployment, and enhance resource utilization across your facilities, ensuring critical equipment is always where it needs to be.
Real-time Performance Monitoring Dashboard
Access live asset performance metrics through intuitive dashboards that display KPIs, maintenance status, and operational efficiency indicators, enabling proactive decision-making and continuous improvement initiatives.
Enterprise-grade Data Governance Framework
Ensure data integrity and compliance with our robust governance system, maintaining accurate, consistent, and secure asset information while meeting industry regulations and corporate standards.
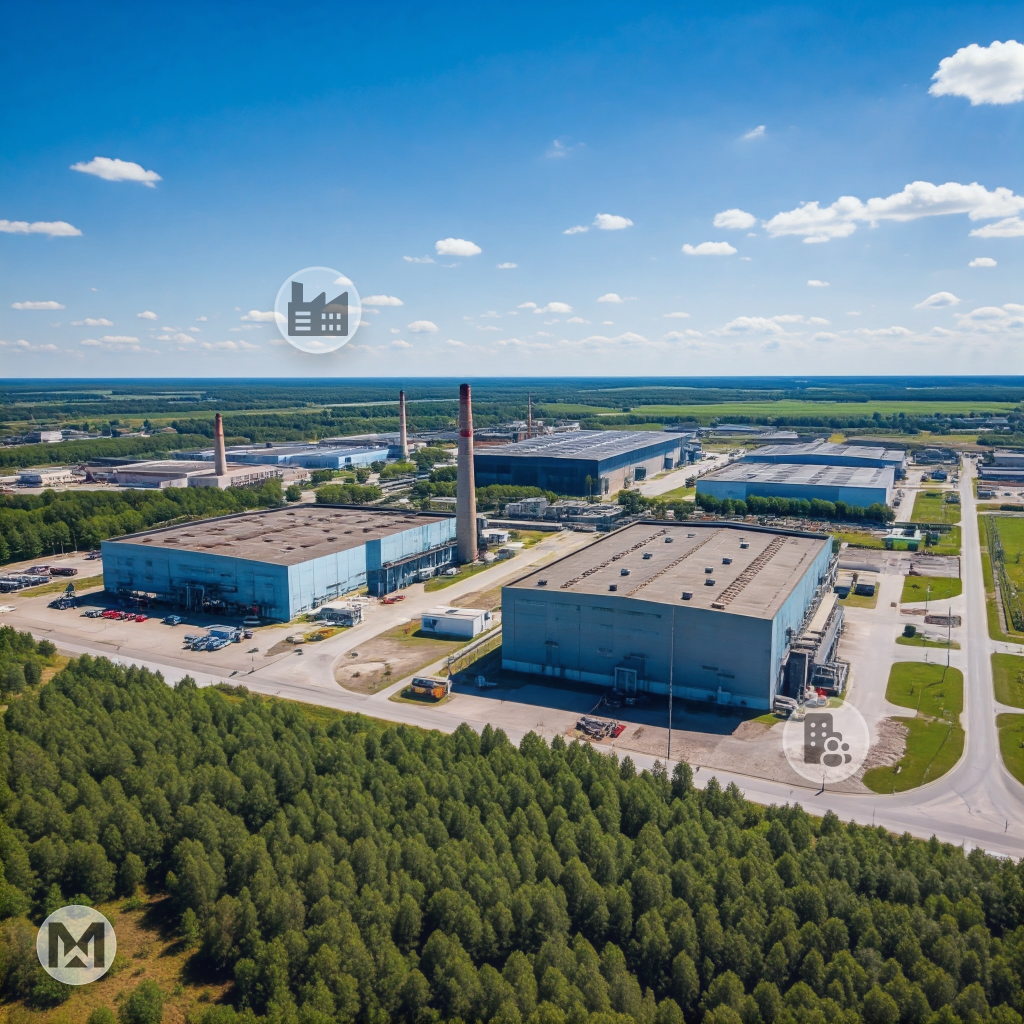
Accelerate Operations with Smart Process Digitalization
Eliminate manual workflows and paperwork with comprehensive process digitalization. MaintWiz's intelligent automation streamlines operations while maintaining compliance and control.
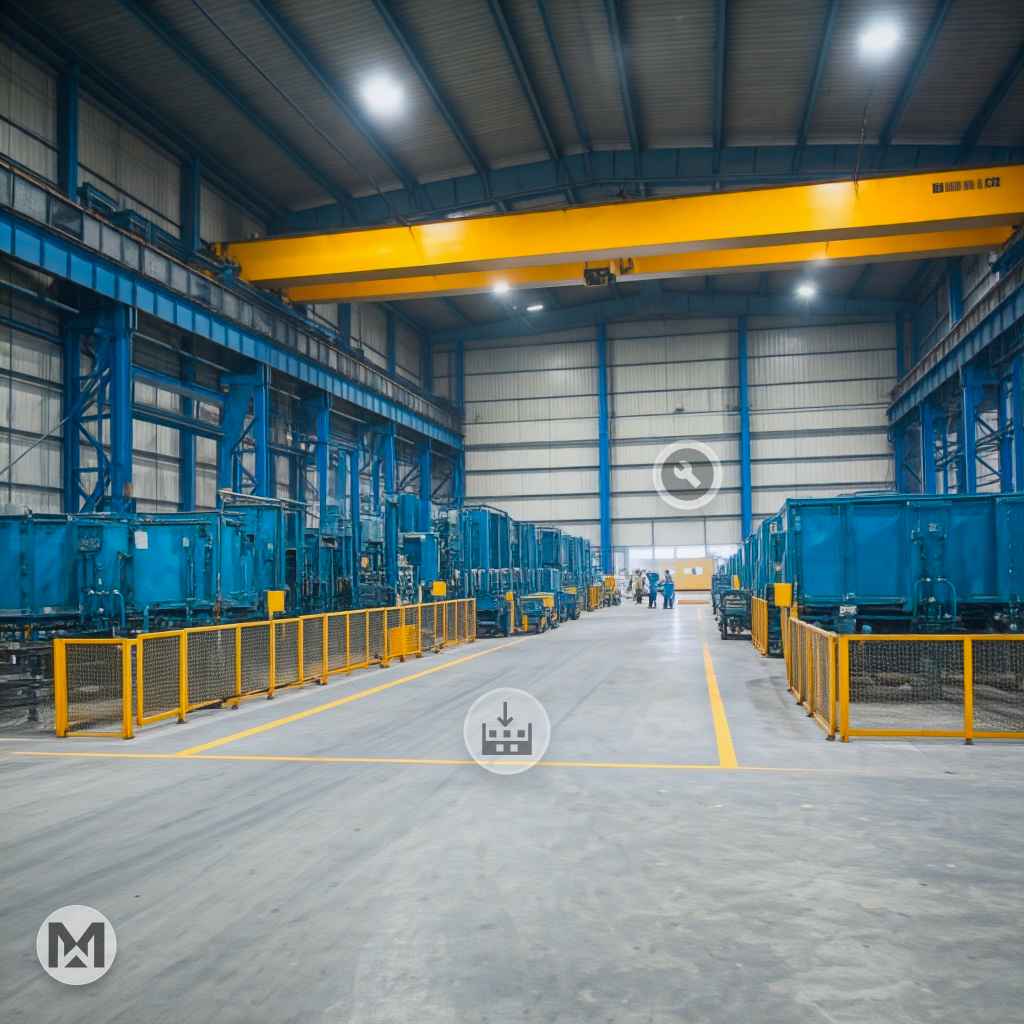
Automated Maintenance Workflow Orchestration
Streamline maintenance operations with intelligent work order generation and scheduling, automatically triggering maintenance tasks based on asset conditions, usage patterns, and preventive maintenance schedules.
Digital Process Documentation and Compliance
Transform paper-based procedures into interactive digital workflows, ensuring consistent execution of maintenance tasks while maintaining detailed audit trails and regulatory compliance records.
Mobile-First Maintenance Management Platform
Empower field technicians with instant access to asset information, work orders, and maintenance procedures through our intuitive mobile interface, enabling efficient on-site task execution and real-time updates.
Real-time Communication and Collaboration Hub
Foster seamless teamwork with integrated communication tools, enabling instant updates, task assignments, and knowledge sharing across maintenance teams, departments, and facilities.
Intelligent Process Automation Engine
Leverage AI-driven automation to streamline routine tasks, from work order routing to inventory management, reducing manual intervention and accelerating maintenance processes.
Advanced Analytics for Process Optimization
Utilize sophisticated analytics to identify process bottlenecks, optimize workflow efficiency, and continuously improve maintenance procedures based on historical performance data and trends.
Speak to a Specialist
Get personalised advice from our experts
Unite Teams with Intelligent Collaboration Platform
Break down operational silos with MaintWiz's unified digital platform. Enable seamless coordination between maintenance, operations, and management teams.
Cross-functional Asset Information Access
Enable authorized stakeholders across departments to access relevant asset data, maintenance schedules, and performance metrics through role-based dashboards, fostering informed collaboration and decision-making.
Integrated Work Order Management System
Coordinate maintenance activities efficiently with our comprehensive work order management system, facilitating smooth collaboration between planners, technicians, and supervisors across multiple departments.
Enterprise Resource Planning Integration
Seamlessly connect maintenance operations with enterprise systems through our robust ERP integration capabilities, ensuring consistent data flow and aligned business processes across the organization.
Role-based Security and Access Control
Maintain data security while enabling collaboration through granular access controls, ensuring team members have appropriate permissions for their roles while protecting sensitive asset information.
Knowledge Management and Best Practices Sharing
Create a centralized repository for maintenance best practices, troubleshooting guides, and technical documentation, enabling knowledge sharing and standardization across the organization.
Interactive Team Performance Analytics
Monitor and optimize team productivity with comprehensive performance analytics, tracking maintenance metrics, response times, and collaboration effectiveness across departments.
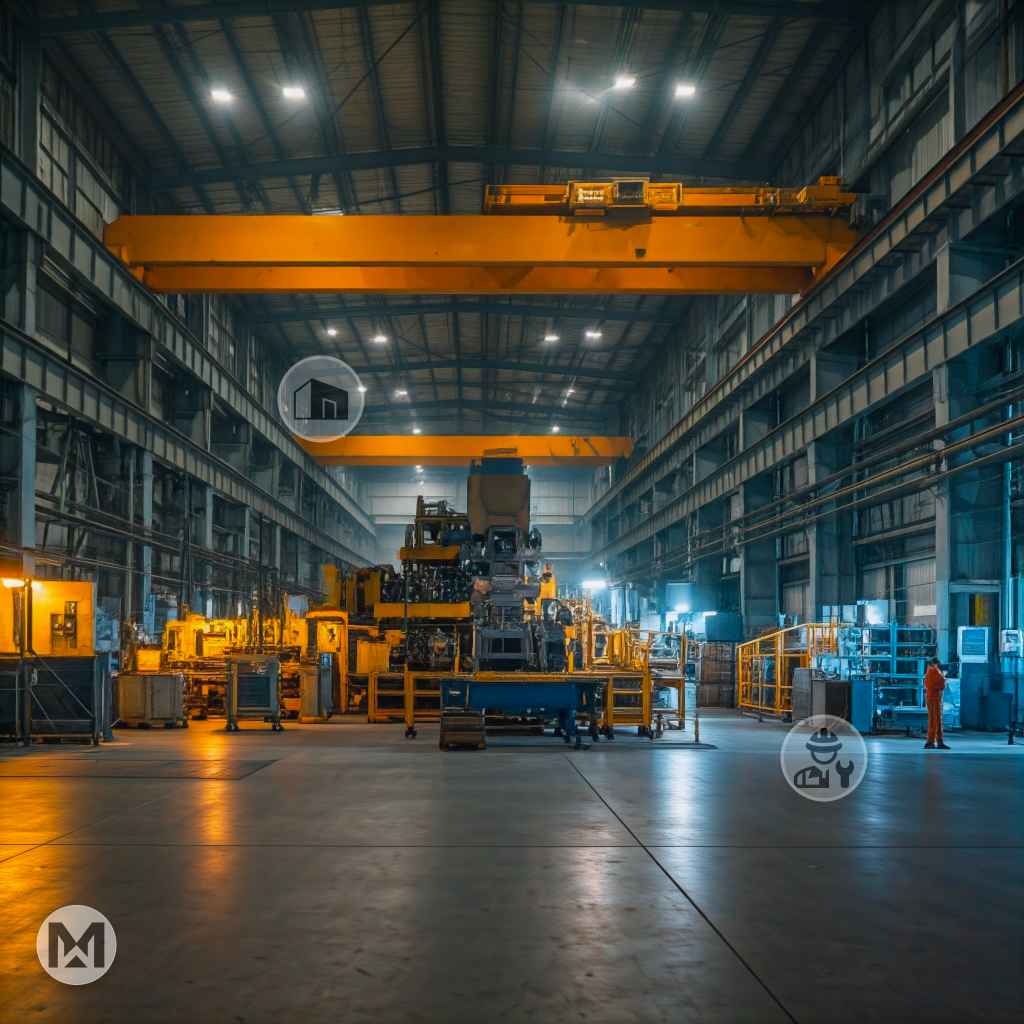
Transform Operations with AI-Powered Asset Intelligence
Harness the power of artificial intelligence and machine learning to optimize asset performance, predict maintenance needs, and drive operational excellence
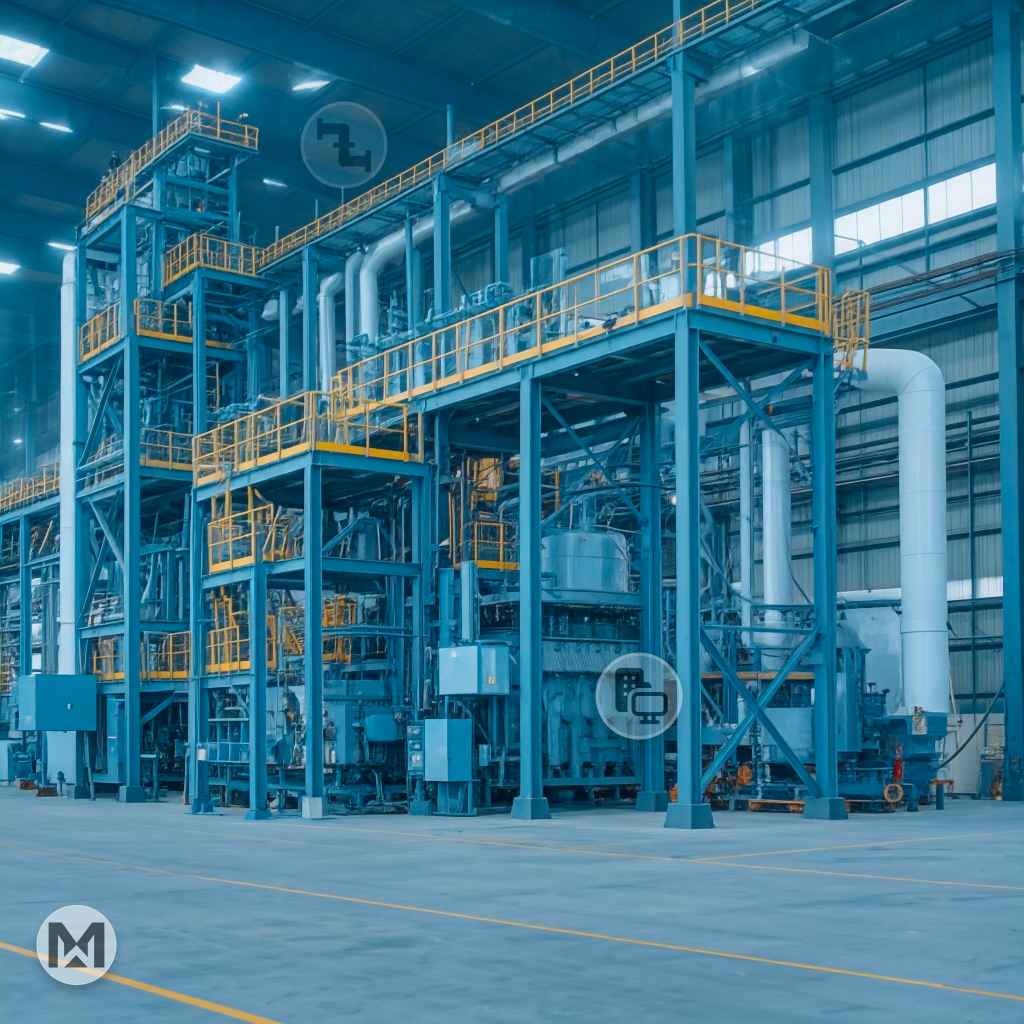
Predictive Maintenance Analytics Engine
Leverage advanced AI algorithms to forecast potential equipment failures, optimize maintenance schedules, and prevent unplanned downtime through early detection of performance anomalies.
Digital Twin Technology Integration
Create virtual representations of physical assets to monitor real-time performance, simulate scenarios, and optimize maintenance strategies through advanced digital twin capabilities.
Machine Learning-Based Asset Optimization
Utilize sophisticated machine learning models to analyze asset behavior patterns, identify efficiency opportunities, and recommend optimal maintenance and operational strategies.
Intelligent Cost Analysis and Budgeting
Make data-driven financial decisions with AI-powered cost analysis tools that track lifecycle costs, predict maintenance expenses, and optimize maintenance budgets based on asset performance.
Automated Performance Monitoring System
Monitor critical asset KPIs automatically through intelligent sensors and analytics, providing real-time insights into equipment health, efficiency, and maintenance requirements.
AI-Enhanced Decision Support Platform
Empower maintenance managers with AI-driven recommendations for resource allocation, maintenance prioritization, and strategic asset management decisions.
Deploy with Confidence on Enterprise-Grade Infrastructure
Rest assured with MaintWiz's secure, scalable, and reliable infrastructure. Our platform adapts to your growing needs while maintaining the highest security standards.
Flexible Deployment Architecture Options
Choose between cloud-based or on-premise deployment models, with hybrid options available to meet your specific security requirements and IT infrastructure preferences.
Enterprise-Grade Security Framework
Protect critical asset data with advanced encryption, multi-factor authentication, and comprehensive security protocols that meet or exceed industry standards for data protection.
Scalable System Architecture Design
Grow confidently with our scalable infrastructure that easily adapts to increasing users, assets, and data volumes while maintaining optimal performance and reliability.
Comprehensive Integration Capabilities
Connect seamlessly with existing IT and OT systems through our extensive API library and integration frameworks, ensuring smooth data flow across your technology ecosystem.
Robust Business Continuity Assurance
Maintain operations with confidence through our comprehensive disaster recovery and business continuity features, including automated backups and failover capabilities.
Automated System Maintenance and Updates
Stay current with automatic software updates, security patches, and system maintenance, ensuring your CMMS platform remains secure, efficient, and feature-rich.
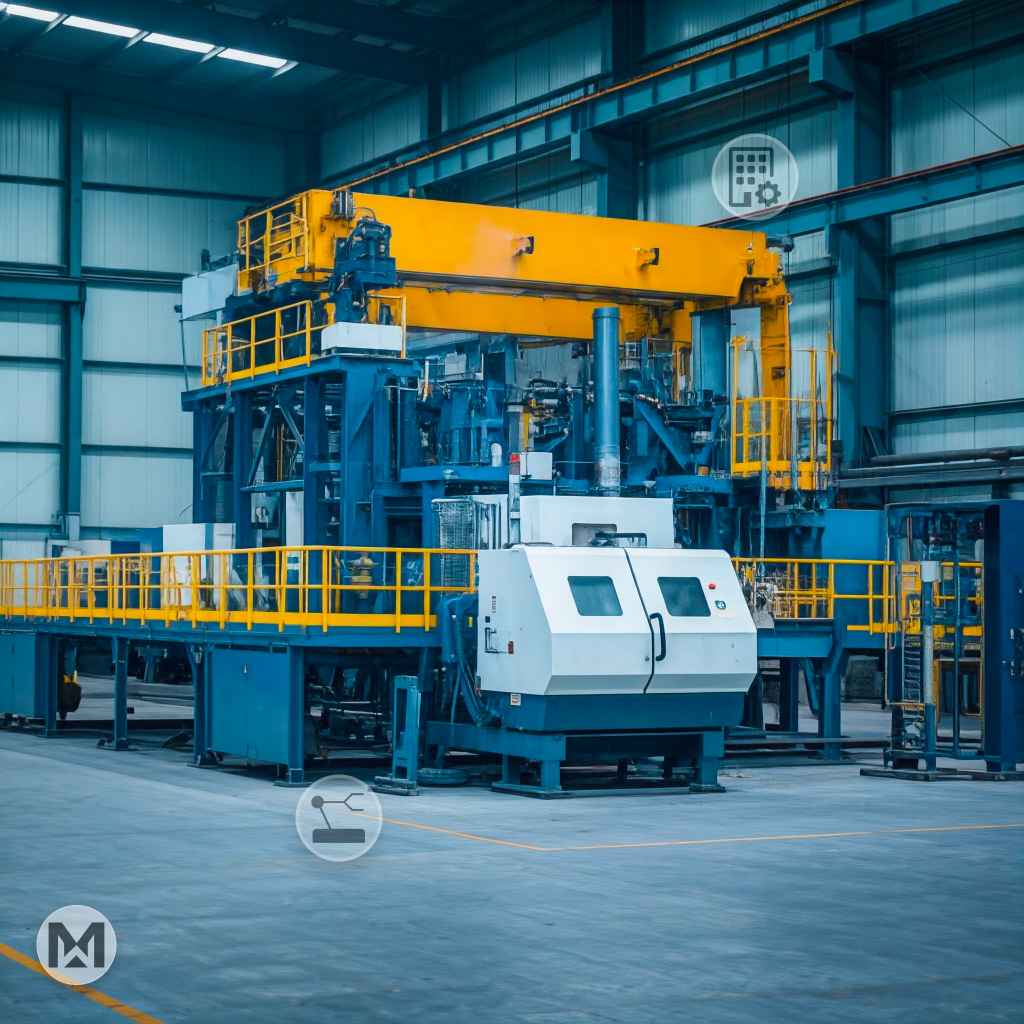
Streamline Operations with Intelligent Automation
Maximize efficiency through automated workflows that optimize resource utilization and ensure timely maintenance execution.
Smart Work Order Management System
Automate work order creation and scheduling based on real-time asset conditions, optimizing maintenance efficiency and resource utilization.
Intelligent Task Prioritization Engine
Automatically prioritize maintenance tasks based on asset criticality, operational impact, and resource availability to maximize maintenance effectiveness.
Dynamic Inspection Management Platform
Generate automated alerts and reminders for scheduled maintenance tasks and inspections, ensuring consistent execution of preventive maintenance programs.
Resource Optimization Intelligence
Automatically assign work orders to available technicians based on skills, location, and workload, maximizing workforce productivity and response time.
Request a one-one demo with our solution engineering team.
Request a one-one demo with our solution engineering team.