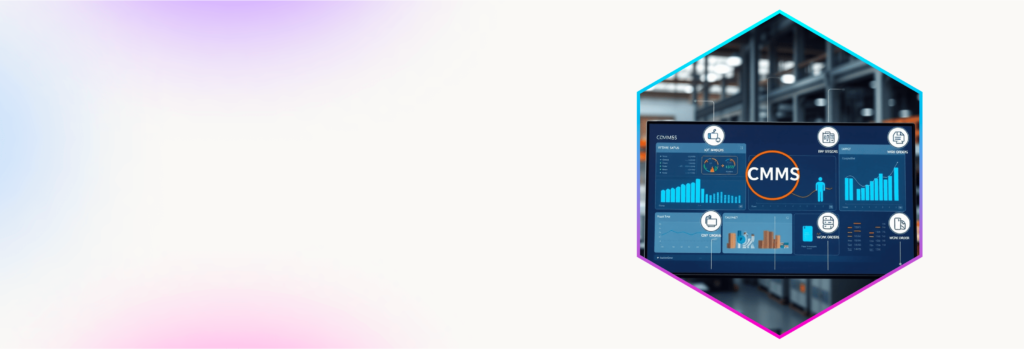
What to Know
About CMMS
Table of Contents
ToggleWhat is a CMMS?
A Computerized Maintenance Management System (CMMS or CMMS Software or sometimes referred to as Maintenance Software) is a software application that helps in streamlining your maintenance operations to achieve maximum operational efficiency. A robust Preventive Maintenance program can be easily managed using CMMS, reducing unexpected breakdowns and optimizing equipment performance.
- Helps maintenance teams manage maintenance-related information better.
- Provides historical information on all the maintenance activities performed on that equipment.
- Helps in creating work orders to attend to a breakdown or to schedule a preventive maintenance activity.
- Digitize the asset information like nameplate details, and technical details, and acts as a repository of design manuals.
- It helps in scheduling preventive maintenance scheduling tasks.
- It can also send out alerts and notifications on breaches of critical parameters like temperature or pressure. Also, it provides insights and analysis about failures and actions taken therein.
- Provides a lot of analytics, performance metrics and historical information over the entire asset lifecycle.
Modern CMMS also integrates with Sensors, the Internet of Things, SCADA and other enterprise systems to provide a unified view of all the operational and maintenance information. By integrating with Predictive Maintenance tools, CMMS can forecast equipment failures and plan maintenance accordingly.
With CMMS, Condition Monitoring data can be collected in real-time, allowing for proactive maintenance measures.
CMMS System Architecture?
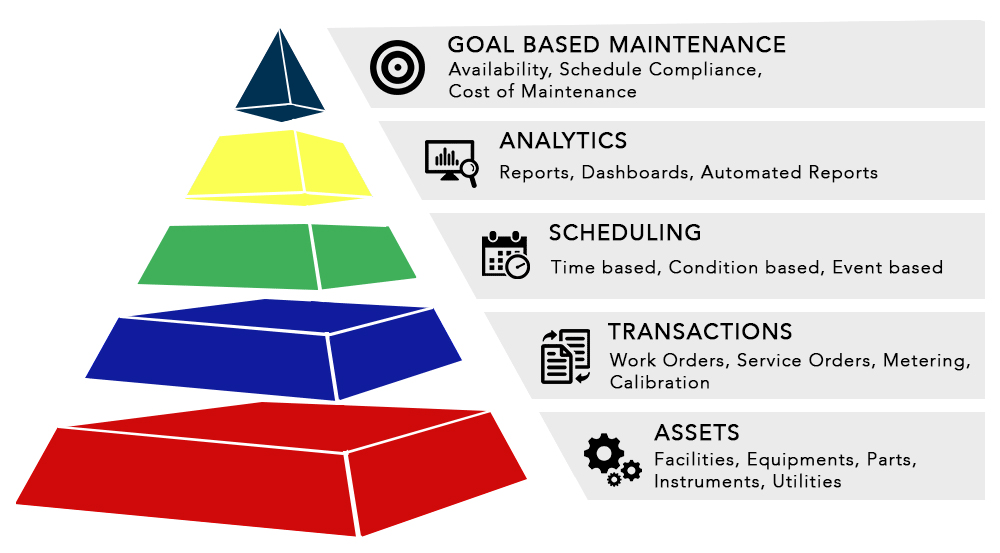
What are the Benefits of CMMS?
Regular maintenance is critical to ensure maximum availability, schedule resources optimally, keep costs down and manage complex operations smoothly. CMMS helps in maintaining the complex asset maintenance required to provide maximum efficiency and reduce downtime. CMMS requirements can assist in identifying repeated failures and fixing the root cause. By setting the root cause analysis and propagating the change across a similar class of equipment, CMMS can significantly reduce unplanned breakdowns, thus reducing the overall cost of maintenance.
Overall Equipment Effectiveness (OEE) is one of the key benefits of using CMMS for maintenance operations.
- Increases Asset Life
- Reduces Downtime
- Improves productivity
- Asset Intelligence – Provides valuable metrics on the operational performance, failure history, financial aspects and risk parameters
- Return on investment (ROI) – Tracks the cost of maintenance, the total cost of ownership, an extra life of equipment, etc. and provides critical information for asset replacement and its timing.
- Helps in audits and achieves excellence in Total Productive Maintenance (TPM), Reliability Centered Maintenance (RCM) and World Class Manufacturing (WCM).
How does the Industry use CMMS?
All industries need their assets to be maintained. Maintenance Software has been used for many years in large organizations, and now with the cloud even Small and Medium businesses are leveraging the power of CMMS for their business benefits. CMMS finds applications across a broad spectrum of industries.
Plant Maintenance
Both discrete manufacturing and process industries require their plant and machinery to be maintained. A single plant spread over a vast area or multiple plants spread over geography.
Facility Maintenance System
Giant malls, high-rise buildings, office campuses, hotels and hospitals, apartment complexes, educational institutions, stadiums and other broad public and private buildings need maintenance.
Power and Utilities
Public utility providers like power generation companies, transmission, and distribution companies, telecom service providers, water supply utilities, etc. run operations 24 x 7 and cannot afford downtime of their critical assets.
Fleet Maintenance
Airlines, long-distance transport providers, cab companies, cargo movers and other logistics providers have a large fleet of vehicles that require routine maintenance. Also, they have complicated equipment in their service stations that need to be maintained too.
Operations and Maintenance
Certain companies specialize in managing Operations and Maintenance (O&M) activities and offer their expertise to other companies. Since O&M is their core business, they need sophisticated systems to manage its daily operations.
How do you select a CMMS?
Full CMMS Solution
Traditional ERPs look at maintenance from a dollar perspective and miss out on the critical daily operational activities needed by the maintenance team. A good CMMS should provide a 360-degree view of the asset and help in improving the productivity and efficiency of the maintenance team.
Ease of Use
Many IT systems fail because they are too complicated for the users. Best CMMS should be simple, intuitive and easy to use. It should have a low learning curve to ensure adoption by the frontline staff.
Mobile CMMS
With mobiles, computing can take to the point of work. Good CMMS embrace a Mobile-first strategy and provide One Click Maintenance. Users can refer entire asset history on tap and should be able to complete all their tasks right at the point of work.
Obsolescence
The maintenance field is evolving as any other field and with more computers coming to the shop floor maintenance is becoming futuristic. Getting stuck with end-of-life software is retrograde as it won’t adapt to your changing needs. Cloud-based CMMS scores here as they update it often with new functionalities and industry best practices.
Reports and Analytics
Metrics drive maintenance. A good CMMS should provide more dashboards, visuals, and analytics and help roll out goal-based support. Emphasis should be on actionable information and focused outcomes.
First Symptom Alerts
Systems should monitor critical parameters to ensure they are optimal. They should warn the maintenance team and management of the first symptoms of breakdown. Forewarning can help rectify issues before the asset breaks down completely, thus saving cost, time and effort.
Quick to Implement
Systems that involve complex processes and long lead times on often get distracted by non-core issues. CMMS should be able to implement in days to help realize the benefits faster.
CMMS ROI
Assets require huge capital outlay and operational expenditure. CMMS can give useful insights on the equipment efficiency, performance metrics, cost of maintenance and total cost of ownership.
Future of CMMS
Technology advancements, the Internet of things (IoT), mobile penetration, a younger workforce and changing business dynamics are all transforming maintenance management. There is continued pressure for improving efficiency, resource utilization, and cost management.
Maintenance Software is no longer restricted to maintenance teams – it’s evolving to become the window to the shop floor. With all the real-time information coming from sensors and the internet of things(IoT), there is an increasing role for CMMS to present a unified view of operations and maintenance, filter the humongous data to provide action-oriented insights and provide alerts and notifications on first symptoms of the breach. CMMS is transforming from a System of Record to a System of Intelligence. With the advent of industry 4.0 technologies, the scope is getting broadened and CMMS is continuously evolving.
Why is MaintWiz the best CMMS for you?
MaintWiz is a new age industry 4.0 CMMS software platform that helps you to digitize your maintenance operations and assist you in converting the routine maintenance transactions to management metrics. MaintWiz is offered as a Software-as-a-Service (SaaS) solution, with mobile enablement to facilitate data capture at the point of work by the operational staff.
MaintWiz is a Simple, Easy to use, Integrated, Cost effective and Scalable solution.
Key benefits of the solution include:
- Cloud-based Maintenance Management solution: Anywhere Access & Ease of Use
- Powerful features to manage work orders for scheduled maintenance or breakdown maintenance – Enhanced Operational Productivity
- Dashboard view: A single window view of the shop floor status. Translate maintenance data to Management Metrics.
- Mobile CMMS Application for shop floor personnel: One Click Maintenance. Access at the point of work
- Easy do-it-yourself data upload and intuitive screens: Concise cycle time to Go-Live and efficient Usage.
- Low Total Cost of Ownership: SaaS offering with a flat monthly subscription fee. No capital expenditure
- Integration: Deep integration capabilities to integrate with ERP, SCADA, Sensors and Enterprise Data Warehouse
MaintWiz is a cloud-based solution, and thus there are no upfront capital investments. It is offered on a Pay as you Grow model with a monthly subscription. Once you sign up, you can start using it on the same day to create work orders and set up preventive maintenance schedules.
Curious about how CMMS can transform your maintenance strategy? Request a demo today to see MaintWiz in action.
Request a one-one demo with our solution engineering team.
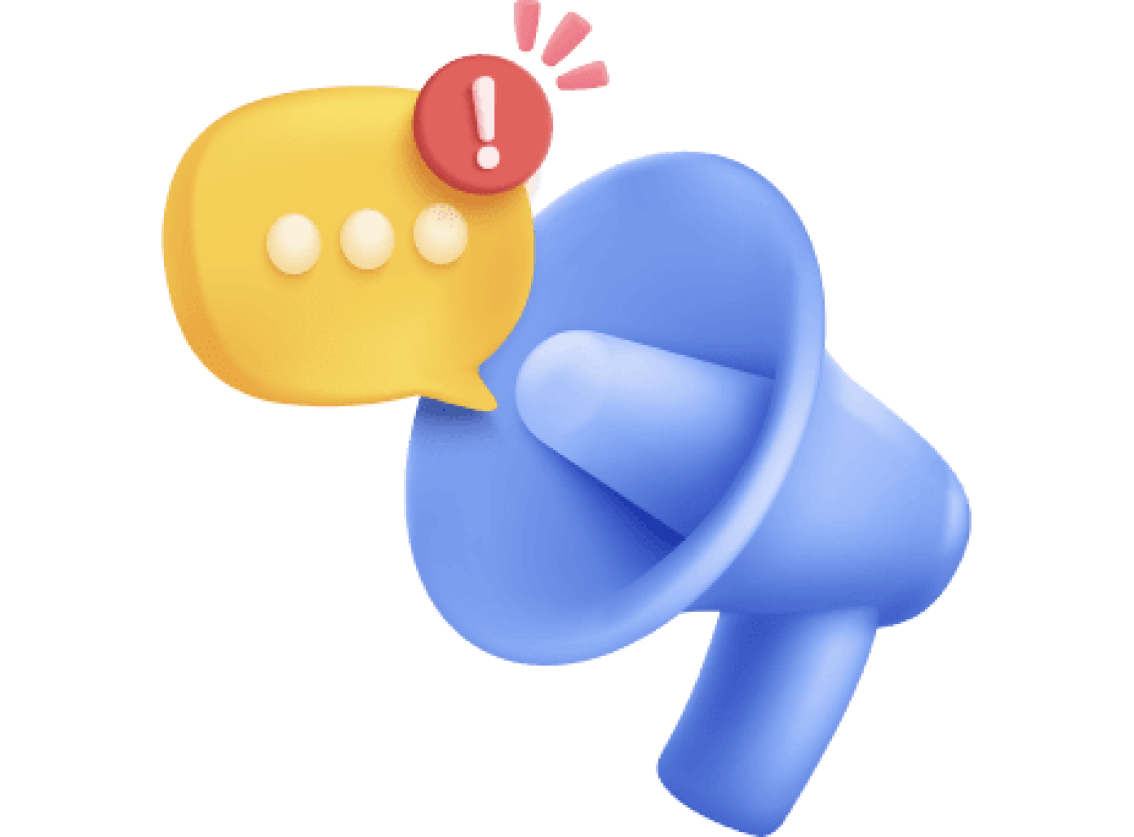
Request a one-one demo with our solution engineering team.