Preventive Maintenance for Protecting Assets
Preventive Maintenance for Protecting Assets
Table of Contents
TogglePreventive Maintenance
What is Preventive Maintenance?
Preventive Maintenance, also known as Preventative Maintenance, is a regular or routine maintenance activity performed on the equipment to reduce the risk of unexpected failure. Preventive Maintenance includes proactive identification of potential failure points, replacement of worn-out spare parts and carrying out general servicing.
Preventive Maintenance is a key component of maintenance strategy and is a sub-set of Maintenance Planning and Asset Management functions. A successful preventive maintenance strategy positively impacts the equipment availability, performance and useful life. Preventive maintenance is also referred to as Planned Maintenance, Periodic Maintenance, Scheduled Maintenance and Preventative Maintenance.
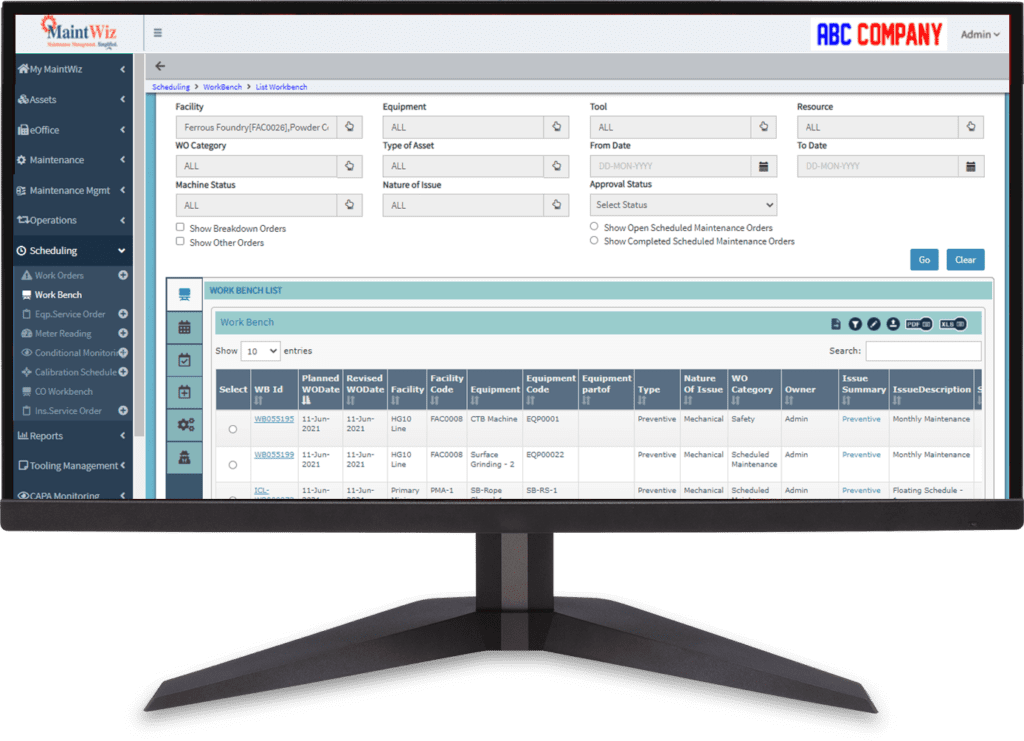
How does Preventive Maintenance differ from Breakdown Maintenance?
Breakdown Maintenance or Reactive Maintenance refers to carrying out maintenance activities after the equipment failure. Reactive maintenance is primarily a break-fix activity executed to repair the failed equipment and restore it back to its working condition. There is no planning or proactive approach involved in reactive maintenance, as the equipment is run-to-failure and thus unplanned downtime is accepted as part of maintenance policy. Breakdown maintenance and repairs are carried out as a reaction to equipment failure.
Preventive Maintenance is a planned maintenance activity carried out proactively (as against reactive maintenance), while the equipment is still in running condition. Regular or routine maintenance is executed at a defined periodicity, to avoid potential failures and unplanned breakdowns of critical assets. Equipment breakdowns are costly, resulting in wasted working hours, sub-optimal use of associated equipment and missed opportunity costs. Therefore the primary goal of preventive maintenance is to avoid such equipment breakdown before it occurs.
What are the benefits of Preventive Maintenance?
The benefits of Preventive Maintenance in plant operations and equipment maintenance are many. Key aspects include
- Improvements in equipment reliability result in higher production and product quality
- Increase of equipment life due to fewer failures and prevention of excessive damage
- Keeping the equipment in good condition increases resource utilization and efficiency
- Reduction of unplanned downtime by resolving problems when they are tiny thereby avoiding costly reactive maintenance
- Ensuring other upstream and downstream equipment on the assembly lines are utilized to their full potential
- Increase productivity, avoidance of repetitive failures and optimization of labour and operational / maintenance costs.
- Institutionalization of the process thereby ensuring repeatability and consistency
- Increase the overall safety of the equipment
What are the different types of Preventive Maintenance?
Different types of Preventive Maintenance include
Time-Based Maintenance
Time-Based Maintenance (TBM) wherein, the preventive maintenance activities recur periodically, based on a specific calendar schedule. Weekly, Monthly, Quarterly, Annual, and biannual scheduled maintenance are examples of TBM. Time-based maintenance is generally a planned maintenance program and is based on elapsed time. Time-based preventive maintenance recurs over fixed intervals, regardless of their usage or performance, in that period. A variant of time-based preventive maintenance is floating schedules, wherein the successive maintenance schedule occurrence will depend on the previous completion. Floating schedules require the earlier scheduled maintenance activity to be complete and the specified time interval has elapsed. With fixed interval preventive maintenance schedules, successive work orders will get generated irrespective of the status of the prior work orders. Floating preventive maintenance schedules avoid unnecessary queueing up of redundant preventative work orders, by imposing an extra condition of prior work order closure.
Usage Based Maintenance
Usage Based Maintenance (UBM) wherein preventive maintenance schedules are based on the equipment usage, rather than elapsed time. Thus, Usage-based maintenance avoids redundant preventative maintenance activities on unused equipment. Usage-based maintenance may recur based on run hours or cumulative production units etc. Usage-based requires a metering mechanism to track the parameter that triggers the preventive maintenance schedule. Such a metering mechanism may be automated and captured directly from the machine interface or manually done via log books. Every time the preventative maintenance work order is generated, the meter is reset or the system is configured to increment the metering interval for calculating the new threshold. Usage-based maintenance is not dependent on the mere calendar and thus an advanced preventive maintenance program, that takes into account the actual usage of the equipment. Usage-based preventative maintenance can occur at different intervals of time, based on equipment usage.
Condition Based Maintenance
Condition Based Maintenance (CBM) wherein preventive maintenance work orders are generated when certain critical parameters breach the specified threshold or control limit. In Condition-based maintenance, the normal operating range for the critical parameters is configured in the system as a business rule. Meter readings of the critical parameters at regular intervals are compared against these business rules. Any discrepancies in critical parameters are treated as a symptom of malfunction and a preventative work order is generated with that issue code. Condition-based maintenance gives alerts on the first occurrence of the symptoms and thus avoids costly breakdowns. They provide sufficient time for the maintenance team to prepare, respond and repair before the equipment failure. That continuously monitor the equipment performance parameters and report to the Condition-based maintenance requires robust operational technology systems like PLC, SCADA, MES, Internet of Things etc. that continuously monitor the equipment performance parameters and report to the CMMS Software
Event-Based Maintenance
Event-Based Maintenance (EBM) occurs upon the incidence of certain events like an annual fire drill, customer visits etc. A set of scheduled work orders will be generated upon the occurrence of the event. Unlike time-based maintenance that occurs on a specific schedule, usage or condition-based maintenance that occurs based on certain parameters, Event-based Maintenance is dependent on external events.
How do you administer a Preventive Maintenance Program?
Preventive Maintenance is a crucial part of any business activity since its principal objective is to preserve the availability of the assets that can use for the business. The preventive Maintenance program follows the Enterprise Maintenance Plan and adheres to the goals and objectives laid out in that.
Preventive Maintenance Planning (Preventative Maintenance Planning)
Efficient preventive maintenance requires careful planning and preparation. Based on the asset hierarchy, equipment grouping and usage conditions, detailed plans including maintenance task checklists, spare parts replacement, and tools required for supporting the maintenance activity described. Preventive maintenance checklists and spare parts replacement schedules are drawn using a combination of the manufacturer’s specifications, operating knowledge and past learnings.
The principal deliverable is to design a preventive maintenance procedure that is comprehensive, adequately, repeatable, and clearly specified granular tasks with estimated duration and optimal recurrence frequency of preventive maintenance.
Preventive Maintenance Scheduling (Preventative Maintenance Scheduling)
Scheduling is a long-range planning activity and includes the recurrence pattern or conditions that trigger preventive maintenance. Scheduling involves defining the business rules that trigger the Preventive Maintenance Work Order to be generated. It’s based on a combination of different types of Preventive Maintenance like Time Based Maintenance, Usage-Based Maintenance, Condition Based Maintenance, Event-Based Maintenance etc. Care should be taken to balance the competing goals of equipment maintenance and optimization of the maintenance cost, time and efforts.
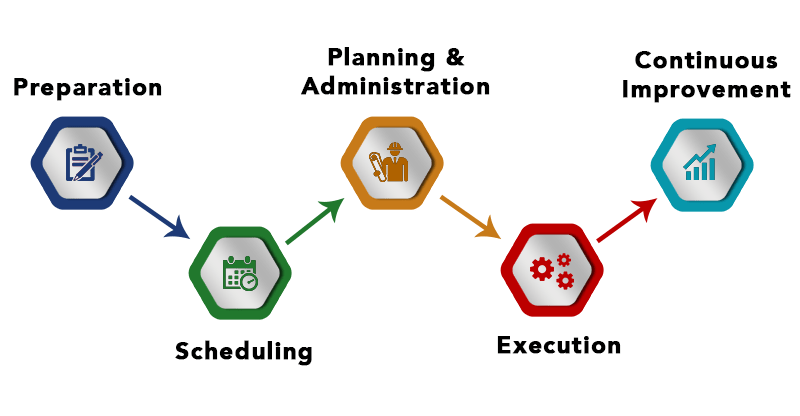
Preventive Maintenance Planning & Administration
Administration of preventive maintenance is based on prevailing on-ground situations, including equipment and resource availability. It includes prioritization of Preventive Maintenance checklists and tasks, adjusting and fine-tuning individual equipment schedules based on their availability, resource levelling to distribute uniform workload and scheduling the activities in such a way it causes the least disturbance to production (eg. holidays, third shift etc.) and communicating to all stakeholders.
Execution
Preventive maintenance execution consists of multiple tasks, often involving cross-functional teams, and has been performed in a specified sequence. For efficient utilization of time and quicker turnaround, adherence to preparatory activities listed in the plan is a must. Includes collecting the spare parts specified, booking standard tools and securing necessary work permits.
Efficient execution requires following the laid out task plan and also ensuring conformance to duration and timeliness. Abnormalities observed, if any, should be reported back for proper analysis and remediation. Adequate handover upon completion and documentation of completion status and spare consumption have followed.
Continuous Improvement:
Ongoing improvements to the processes, operational tasks, schedules, etc., based on the learnings from the history and industry best practices help to institutionalize the knowledge and standards and to roll out a world-class preventive maintenance program. Includes definition and tracking of metrics, identifying opportunities for streamlining the practices, eliminating waste and deploying horizontally.
Horizontal Deployment is the process of sharing the learnings and best practices in maintenance management laterally across the organization. In the preventive maintenance context, the improvements made for specific equipment to avoid a potential breakdown can be copied over to all the other peer class equipment. Thus it propagates peer-level learning and avoids expensive failures and unplanned downtime.
Define Preventive Maintenance Life Cycle
PM Life Cycle defines the stages that a preventive maintenance process goes through as it proceeds from initiation to completion.
What is Preventive Maintenance?
- Preventive Maintenance programs for each equipment or group of equipment are defined in line with the Asset Management Strategy, Maintenance Strategy and Maintenance Planning.
- Each piece of equipment can have multiple preventive maintenance Schedules. Each of such preventive maintenance schedules shall be independent of each other and have its own preventive maintenance checklists and spare replacement tasks.
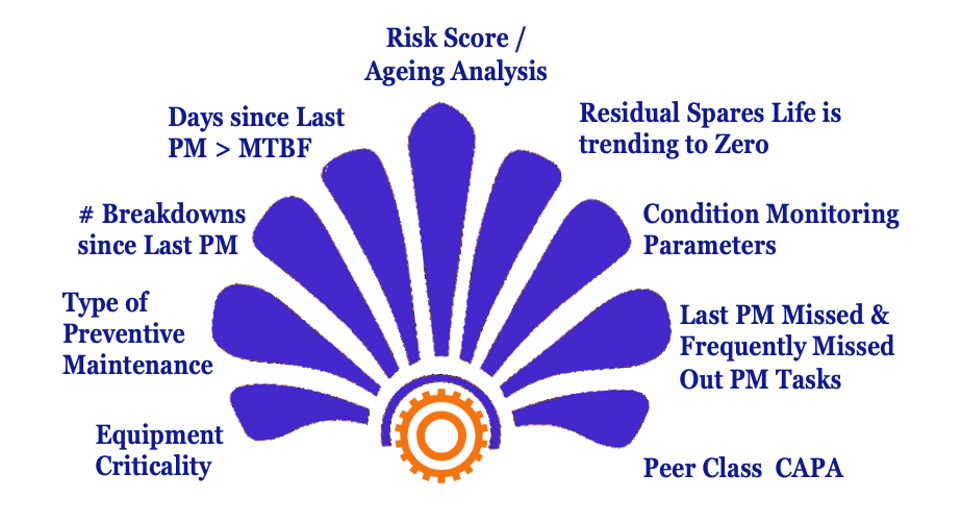
- A preventive maintenance schedule can have business rules based on time, usage, condition or event-based triggers. Based on the nature, preventive maintenance checklists and tasks may vary.
- Upon the condition being met, the preventive maintenance work order shall be generated.
- The PM Work Order will inherit the preventive maintenance checklists and tasks, recommended spares change, common tools required (eg. crane) etc. from the parent preventive schedule.
- A preventive maintenance work order will be assigned to a maintenance technician and get executed and follow the work order life cycle.
- Preventive Maintenance analytics like PM Compliance, PM Effectiveness, Overdue tasks, Task completion percentage, preventive maintenance cost etc. are available for analysis and further actions.
- Planning tools help give an overview of all the Preventive Maintenance Work Orders to be generated over a planning horizon and help planners to adjust the current instance of preventive work order based on equipment availability, resource loading, spares availability, vendor coordination etc., without impacting the parent preventive maintenance schedule
Manufacturing organizations have thousands of equipment that fall under different plants, units, lines, equipment grouping etc. Usually, the plant maintenance teams standardize the preventive maintenance programs for each equipment class and roll out. Customizations based on equipment criticality, operating conditions, failure history etc. are suitably incorporated. Planned Maintenance programs were used to run out of log books and Excel spreadsheets but now most organizations use CMMS software or Enterprise Asset Management systems.
What is a Preventative Maintenance schedule?
Preventative Maintenance schedules (Preventative Maintenance schedules or PM schedules) refer to the timing of the execution of the planned maintenance activities. Schedules refer to the recurring pattern in which the preventative maintenance work order will be generated for specific equipment based on the trigger conditions defined.
In addition to these trigger conditions, preventive maintenance schedules will also contain the specific asset details, the list of jobs that need to be completed (preventive maintenance checklists), sequencing of steps, if any, and assignment details like individual or group who will execute the job.
Preventative maintenance schedules may also contain the spares that need to be changed, maintenance and safety instructions, work permits to be procured, common tools required (eg. Cranes, forklifts etc.), vendor coordinate required if any and shift in which it needs to be carried out. Preventive Maintenance Schedules are configured as a parenting schedule with all the details and when the trigger conditions are met, preventive work orders are created by the system automatically with all underlying details and assigned to the relevant person or group.
Examples of Preventive Maintenance schedules include
- Visual inspection of the equipment and cleaning on Monday, Wednesday and Friday every week
- Changing Oil fortnightly on every alternate Tuesday
- Monthly maintenance on the 8th calendar day of every month
- Oil inspection and analysis to be carried out on the third week of every calendar quarter
- Inspection by equipment manufacturer once in 4 months, from the month of installation for a period of 5 years, as a part of warranty services
- Vibration analysis of equipment to be carried out every six months
- Annual Safety audit to be carried out in the month of April every year
- Shut-down maintenance to be carried out every 4th year, starting 2018
- 365 days from the completion of the prior preventive maintenance work order
- Upon completion of every 5000 run hours of the equipment starting at 45000 hours
- Upon breach of control limits for the specified condition monitoring parameter
What is a Preventative Maintenance task list?
Preventative Maintenance task lists (PM task lists), sometimes referred to as Preventive Maintenance Checklists, PM Checklists, PM Sheets or Job Plans, are the list of tasks that need to be executed and the inspections to be carried out, to complete the Preventive Maintenance. Preventive Maintenance checklists will define who (assignment), what (task name), when (sequence, if any), how (task details and spares to be replaced) etc. Advanced maintenance management practices include additional attributes like criticality of the maintenance task, sequencing of tasks and mandatory or non-mandatory nature of the activity.
What kind of maintenance activities can be scheduled?
Many different maintenance activities that need to recur at a set pattern can be scheduled. Scheduled maintenance activities include
- Work Orders to carry out preventative maintenance tasks and spare parts replacement
- Calibration of instruments to meet statutory compliance
- Service orders to complete the cleaning, lubrication, tightening and adjustment of the equipment
- Inspection orders to evaluate the condition and/or performance of equipment and its assemblies. Other types of inspections include building inspections, electrical inspections, plumbing inspections, structural inspections, certification inspections etc.
- Safety inspections or Safety audits that include a structured and systematic assessment of various potential hazards in the work environment, risk analysis and the efficacy of mitigation plans
- Specialized maintenance activities like vibration analysis, oil inspection etc. can also be scheduled
- Major maintenance activities like management of change activities like overhauls and upgrades, capacity additions, energy management projects, shut down maintenance etc. can also be planned and scheduled.
How do you measure the efficacy of Preventive Maintenance programs?
Key Metrics that are used to measure the Preventive Maintenance programs are PM Compliance:
Preventive Maintenance Compliance (PM Compliance or PMC or Schedule Compliance) is the rate of completion of Preventive Maintenance schedules. It is measured as the number of preventive maintenance activities completed to the total number scheduled in a given period of time and is expressed as a percentage.
PM Effectiveness:
Effectiveness is the capability of producing the desired result or the ability to produce the desired output. This Preventive Maintenance to be effective has to meet the intended business outcome of preventing breakdowns. Preventive Maintenance Effectiveness (PM Effectiveness or PME) is an indicator of the degree of success or its likelihood of achieving the desired result.
What is Shutdown Maintenance?
Process industries run continuously and thus isolated preventive maintenance without impacting the more extensive operations is difficult. Planned maintenance for such sectors involves a shutdown of the entire services to facilitate preventive maintenance activities. Shut down maintenance is referred to as Turn Around maintenance (TAM) also.
The scale of operations, complexities and interdependencies demand a great deal of planning to determine what needs to be shut down and in what sequence, and what must be done during the shutdown, what may be done to restart the plant and resume operations, including contingency plans, and what can be done after the restart.
Shutdown maintenance is done once in a few years and preparation and planning draw extensively from history, statistical techniques, risk analysis, project management and coordination.
How does a CMMS help in rolling out Preventive Maintenance programs?
Computerized Maintenance Management Systems (CMMS) help in digitalizing asset management and plant maintenance. They can build a comprehensive asset register with all the details of the facilities and equipment, including technical specifications, asset grouping, cost centre, maintenance history and performance parameters. CMMS, due to its versatile functionality, may often be referred to differently as CMMS software, enterprise asset management software, maintenance management software, preventive maintenance software, preventative maintenance software, equipment maintenance software, work order software etc.
CMMS software can also digitalize all the process assets like maintenance policies, maintenance plans and procedures, preventive maintenance manuals, PM schedules and job plans, PM compliance metrics, PM planning activities and other maintenance records. CMMS software can also host OEM recommended PM schedules and task lists, as well the preventive maintenance programs of peer class assets. Both of these provide significant referral value while defining effective PM programs for equipment.
Specific benefits of having a CMMS system in the Preventive Maintenance program include
- Ease-of-use and quick set up of preventive maintenance schedules and task lists
- Support time-based maintenance, usage-based maintenance, condition-based maintenance and event-based maintenance programs
- The equipment repository has historic information and fault history, which can be a good starting point
- Provides rich tools sets to plan, track and administer preventive maintenance programs effectively
- Automated creation of preventive work orders when the set conditions are met and assignment to the right maintenance team member for execution
- Instant access of all maintenance records for the maintenance technician via mobile and on-the-spot completion of work order entry
- Visibility of spares availability and planning spares procurement for upcoming preventive maintenance activities
- Comprehensive maintenance metrics including PM Compliance, incomplete tasks, PM effectiveness, KPIs, Cost of Maintenance, maintenance budget vs actuals etc.
- Standardization and institutionalization of maintenance processes and metrics across the enterprise
- Improvement in people productivity, equipment efficiency and workplace safety
- Ensuring regulatory compliance and adherence to industry standards and best practices. Industries like Aviation (Title 14 Code of Federal Regulations – CFR Part 43, CFR Part 91 etc.), Pharmaceutical (US FDA Title 21 Code of Federal Regulations – CFR Part 11, Good Automated Manufacturing Practices – ISPE GAMP) and Oil and Gas (ISO 14224:2016) have well-defined guidelines, standards and regulations that they need to adhere to.
Future of Preventive Maintenance
Preventive maintenance programs started with simple planning exercises with wall charts and card indexes. Visual schematics, project plans, process diagrams and colour codifications aid in the simplification of preventative maintenance planning and execution. History cards, job control, safety and sustainability procedures and past learnings were used to improve effectiveness. Total Productive Maintenance (TPM) has Planned Maintenance as one of the eight pillars and places a lot of emphasis on preventive maintenance to improve plant efficiency.
Earlier maintenance organizations were using manual processes for managing all their maintenance activities including scheduled maintenance. PM has primarily driven out of paper-based processes (PM planning boards, log books etc.). The manual process was tedious and not efficient. Later larger plants went for computerization with maintenance software installation. Computerized Maintenance Management Systems (CMMS) helped in streamlining the various equipment maintenance activities and also getting maintenance metrics.
While early CMMS systems tend to focus more on preventative maintenance scheduling, resource management and inventory, they were still silo applications and functioning in a stand-alone mode, catering to local needs. It was predominantly transaction-oriented and a holistic view of the entire plant and equipment was missing.
Advancements in industry 4.0 technologies have brought in real-time integration with operational technologies. This has resulted in automated capture of performance data of critical parameters and enabled conditional monitoring and maintenance capabilities in CMMS systems. Technological advances in real-time data capture, large-scale and cost-effective storage systems and analytics enabled quicker adoption of condition-based maintenance across industries. Simultaneously the significant shifts in the cloud, analytics, and mobile technologies made such sophisticated cloud-based CMMS software available for even small and medium organizations at affordable costs.
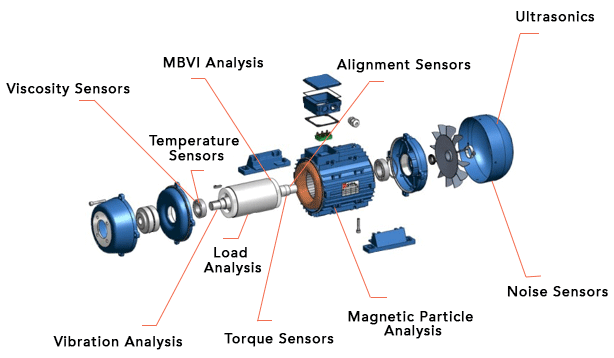
Breakdown Maintenance | Preventive Maintenance | Predictive Maintenance | |
---|---|---|---|
Focus | Fix failures after they occur | Avoid failures | Forecast failures Control |
Triggers | Equipment breakdown | Run hours Elapsed calendar time Breach of critical parameters | Statistical analysis Trend deterioration Actions arising out of predictive algorithms & sophisticated equipment modeling |
Enablers | Troubleshooting Maintenance support | Maintenance checklists | Condition Monitoring SCADA, Internet of Things |
Maintenance Behaviour | Run to failure Reactive | Organized and Systematic | Optimized and Futuristic |
Condition monitoring has become ubiquitous today with most equipment manufacturers providing data access to critical parameters. CMMS integration with sensors, programmable logic controllers (PLCs), SCADA, smart devices and other automated sources of data capture is leading to a data explosion. Humongous data inundation has shifted the focus of tools from consumption to management by exception and action-oriented insights.
Real-time data availability simultaneously from multiple types of equipment has led to application of Artificial Intelligence / Machine Language (AI/ML) technologies to model the system behavior more accurately. Powerful algorithms and system modeling is redefining modern shop floor and leading to a holistic understanding of equipment, operating conditions and helps us predict their failures. Predictive maintenance is transforming maintenance planning and asset management. Preventive maintenance has its utility and thus most organizations are adopting a hybrid maintenance strategy, wherein preventive maintenance will continue to co-exist with other types of maintenance management practices, like reactive maintenance and predictive maintenance.
Why is MaintWiz CMMS an ideal solution for managing your Preventive Maintenance programs?
MaintWiz is a new age industry 4.0 CMMS software platform that helps you to digitalize your maintenance operations and records, and assists you with powerful tools to manage Predictive, Preventive and Breakdown Maintenance programs. MaintWiz is a Simple, Easy to use, Integrated, Cost effective and Scalable solution.
Key benefits of MaintWiz in designing and administering Preventive Maintenance plans include:
1. Robust feature set to manage the entire preventive maintenance program, including scheduling, checklists, spare parts, tools management, resource management and tracking. Complete maintenance records are available at a single place and on-demand.
2. Comprehensive scheduling capabilities to match the unique maintenance policy needs of every industry. Support time-based maintenance (fixed and floating), condition-based maintenance and event-based maintenance.
3. Sophisticated functionalities under the hood are simplified for the user, with easy-to-use excel uploads. Excel uploads support schedule setup, and task lists to design and spare parts recommendations. Copy paste functionality to copy assignments over from past work orders is also available.
4. Planning Workbench for effective PM program execution: Adjusting the preventive maintenance work orders generated out of the long-range scheduling to meet short-term, tactical on-ground realities without impacting the master schedules. PM plans can be optimized based on equipment availability, resource levelling, spare parts and tools availability, Vendor, AMC / Warranty service provider visits etc.
5. One-click maintenance to help the maintenance team complete their preventive maintenance tasks at the point of work, via a mobile app.
6. State-of-the-art analytics and interactive reports to monitor preventive maintenance compliance, cost of preventive maintenance, horizontal deployments and more.
With MaintWiz industry 4.0 CMMS, there are no entry or exit costs. It’s offered as a Software-as-a-Service (Cloud-based CMMS) on a monthly subscription basis. Excel templates-based data upload enables you to start quickly on Day 1. Experience the complete power with Zero Capital Investments and Zero Implementation Time.
Request a one-one demo with our solution engineering team.
Request a one-one demo with our solution engineering team.
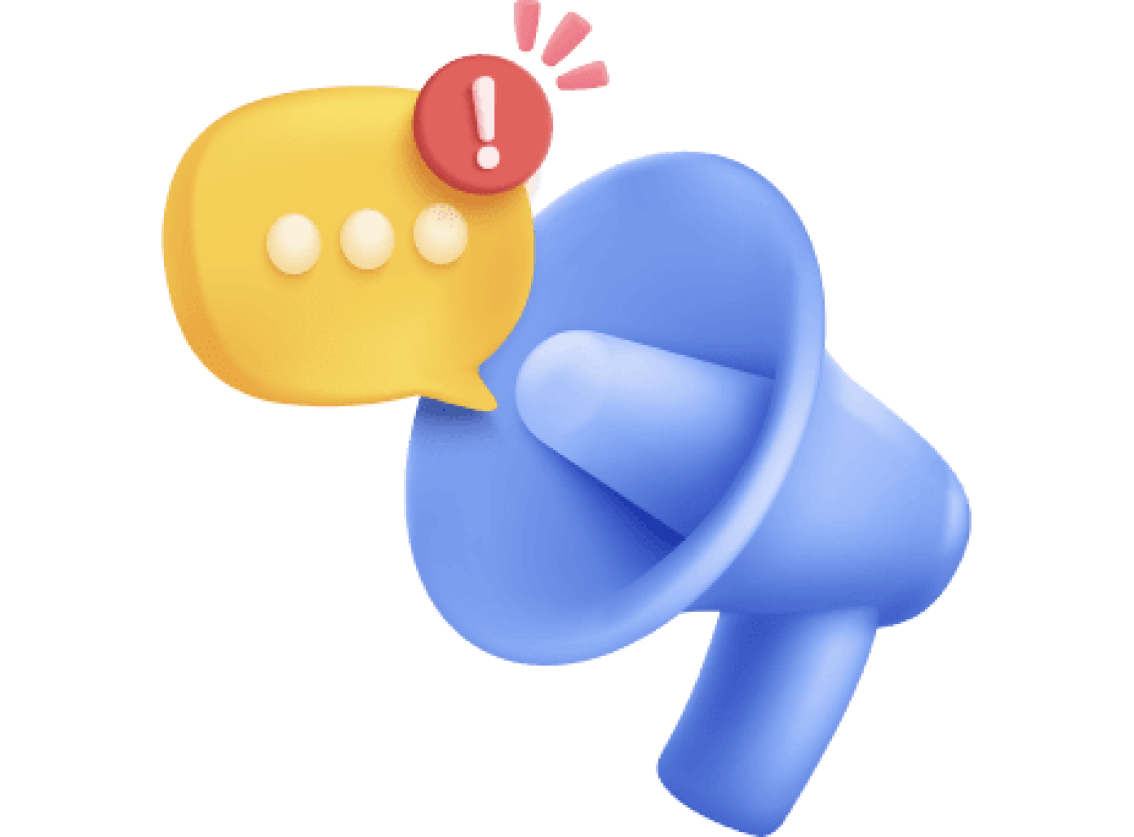
Company